2021-08-17
Utah Business: Space travel is closer than you think
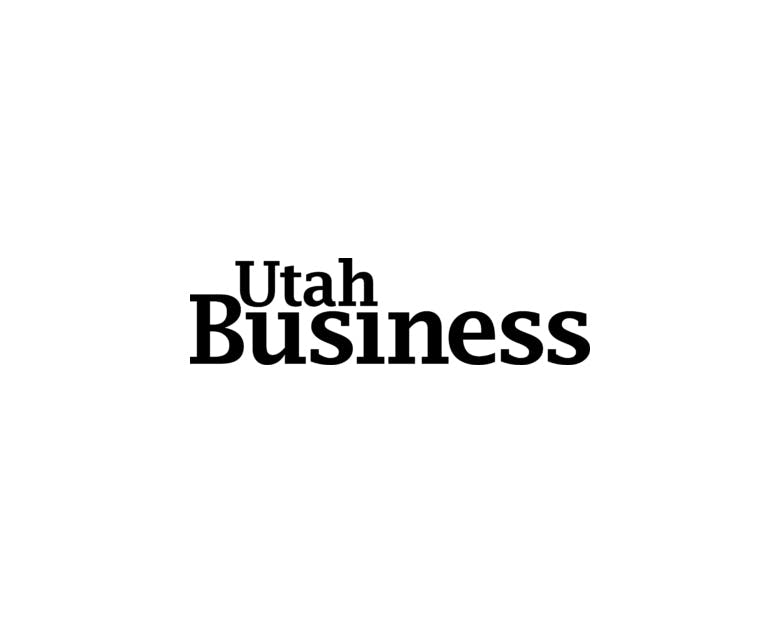
Intergalactic in the news
By Jacqueline Mumford
"Science fiction inspired a lot of the technology we’re developing now. It’s not fiction, really: it’s what we’re doing,” says Brian McCann, CEO of Intergalactic. He’s one of the people taking ideas off the page and into the real world.
RAM Company is the brain behind Intergalactic, acquiring Airborne Environmental Control Systems and relocating the company to St. George in 2019. Airborne started making inroads reducing heat levels in aviation production and McCann, along with the rest of the RAM team, saw this firm foundation as an opportunity to shoot for the stars.
Literally.
Aerospace innovations inspired by Formula One racing
Intergalactic’s foundational innovation is their thermal management systems: the way computers, cars, and aircraft alike keep from exploding.
“The systems we have now have at their core, are technologies from the 1950s and 60s,” McCann says. “They just can’t meet the heat load that we’re bumping up against now. We’ve developed, tested, and sold a system that’s 300 percent more efficient than anything else on the market.”
Their product’s base design is inspired by precision cooling technology—the stuff used by your car’s AC and keeps your house comfortable in the summer. The rest of the system was constructed from a handful of other preexisting ideas—from lines of code in Silicon Valley’s AI to Formula One racing’s microchip heat exchangers––that had never been applied to the aerospace world before.
“We knew that Formula One racing needed to cool entire cars quickly and consistently, and although what they do and what we’re doing is pretty different, we shared that same need,” McCann says. “We were able to pull stuff like that from a bunch of different places because of our core management team’s experience in the industry––we’re combining modern tools with our career-long experience in aerospace to build better.”
An Intergalactic-branded thermal heat system doesn’t just mean better AC in a fighter jet –– it creates faster leaner and smarter aircraft.
“Once the system is installed, it automatically adjusts to make itself more efficient,” he says. “It’s coded and tailored to Department of Defense standards, so not only is it secure and able to be maintained from far away, but it can also monitor its own use, communicate to users what levels it’s operating at and give advice for cleaner operation.”
This Siri-esque tech is revolutionary in the aerospace realm, but it’s only the beginning for future advances: the engineering team is using it as a springboard to supersonic flight…
Figuring out faster―and safer―space travel
…and Mars.
“With this critical layer of innovation, sure, we can make our planes and jets fast enough to fly from Los Angeles to London in three hours––but what’s really cool to us is the increased ease of space travel.”
McCann says with the right heat management system in place, space flight can be faster, and therefore safer. “It takes a while for the body to adjust to a change in gravity and spending too long away from Earth can do real damage to your heart, your nervous system. This new infrastructure can speed up the trip, slowing the potential damages and making travel less dangerous.”
Already miles ahead of many of their competitors, space is where McCann has his targets set next.
“We’ve cleared the baseline with heat management,” he says. “And we can tailor the system to apply to anything that uses heat―like cars, buses, trains. But the space economy, that’s where this industry is headed. We’re working with multiple space companies now because we want to be part of it––the idea of space camps or quick flights around space sounds really, really cool. The idea of making that space travel safer was what drew us into an acquisition and a change of name, and now we’re making it possible.”
Using data visualization to speed up innovation
The jets, planes, and spaceships aren’t just gaining speed––the development also has its foot on the accelerator. “The Joint Strike Fighter, a recent fighter jet, was first conceived in the mid-90s,” McCann says. “It didn’t end development until the early 2000s and finally went into production in 2015. That’s at least a 15-year process.”
This process is dotted by trial and error, and the team often has to go back to square one. “We’ve been using old school methodologies, designing products and ideas in isolation––the production and testing are separated, where we design, then test, in a circle. And when new or better technology comes along, we’d often scrap what we’ve done and start over,” he says.
Pointing to reports of the US Airforce’s ability to design, build, and commission the same type of fighter jet in a year, McCann says this kind of product development process is a thing of the past.
For its part, Intergalactic is kicking things to turbo speed, too, when it comes to its smart systems.
“We took the system design process, something that’s traditionally a 10-year part of development, and condensed it to three to four years,” he says. “We built it really, really fast, but we also built it better. Our performance was audaciously better than anyone else’s in the markets––so much better that we turned heads.
“Multiple major companies like Boeing, Raytheon, Lockheed Martin said ‘no way that’s accurate.’ The thing is, we’d already built, tested, and analyzed the data from the systems. We invited them to come look at it, and even after seeing the results, they’re still shocked that something like what we’ve done is even possible.”
Intergalactic has secured a government contract to build between 1,800 and 5,000 of these systems over the next 15 years, with more deals in the distance. And McCann says all this creation is possible through the utilization of data visualization.
“Computers can’t design something like our systems from a blank sheet,” he says. “But they can run millions and billions of simulations to point us in the right direction. We’ve used data analytics to test different types of materials to see if they can withstand pressure, figure out thermal properties, and understand things from a magnetic perspective instead. They even simulate fighter jet vibrations. We can know before we’ve even created the physical object almost exactly what it’s going to handle like.”
The data collected from running these tests identify weaknesses and strengths of the design, cutting out the middleman part of the trial-and-error process––you know, building an entire system just to find out one small part was wrong.
“This change in thinking, the ability to accept the data analytics world, it’s how we built our thermal management systems, and how we’re going to keep innovating at this pace,” McCann says. “There’s a lot of incrementalism in aerospace. It’s a process of just notching your way up, being slightly better than last time, and that’s all that’s expected from you.
“We’re still creating aircraft the way we did decades ago, with oil, belts, and analog. We think just because that made sense before the Vietnam War doesn’t mean it makes sense today, and we’re not accepting that over here.”
Northrop Grumman’s race to staff the digital world
Intergalactic isn’t the only aerospace company leaning into the digital world. Northrop Grumman, based in Roy, is another one of the firsts to integrate virtual modeling into its contracted gigs.
Northrop finalized an agreement to work on the Ground-Based Strategic Deterrent, the US Airforce’s weapon system replacement for an aging ballistic missile system at the end of 2020. The contract will focus on modernizing the existing approach to the ground-based leg of the land, sea, and air “nuclear triad.”
To meet this redesign of an integral part of America’s national security, Northrop had to go digital.
“This is the first large-scale program that the government has identified as a theory program, what they call the ‘Trinity’ of digital innovation,” says Greg Manuel, VP and general manager of the Strategic Deterrent Systems Division for Northrop Grumman. “With digital innovation, we’re also speeding up our development processes and making our jets faster and more efficient in one move.”
The trinity involves a lot of the same work McCann and Intergalactic are employing simulations run on large digital interfaces to test ideas more quickly. As this part of the development process becomes more computer-driven, jobs aren’t disappearing––they’re exploding in almost every department.
“We need data scientists, designers, writers, software developers,” Manuel says. “We need agile coaches, hardware designers, people who can understand how to work in a 3D computer drawing. There’s not a single type of skill that we’re not looking for during this shift away from traditional system engineering.”
These new hires––of which Northrop expects to add monthly until the end of the year––will fill a few new buildings on the company’s campus. One of these, the Integrated Test Facility, is planned to be 320,000 square feet, and dedicated entirely to running simulations and testing data, like Intergalactic.
Limitations of the “old” aerospace world
If the technology and development processes are clearly outdated, then why are Utah’s aerospace engineers some of the first to shift to data analytics? How could Intergalactic’s thermal management system be revolutionary––with the same access to these resources, shouldn’t everyone be building things just like it?
McCann thinks all this tech was left on the table by a cliquish, too risk-averse industry.
“Aerospace, intentionally, is a club that’s really hard to get into,” he says. “And like a lot of popular clubs, they want to see two things: millions of dollars and of things with your name on it, like patents. Intergalactic’s parent company, RAM, spent its first 25 years just trying to get a spot. It’s a model that chases people away.”
Even for those who got the golden ticket, working for large aerospace companies was still unfulfilling. Intergalactic was able to recruit engineers, usually from leadership positions at Fortune 500 corporations, to work for RAM’s acquisition with the promise of a more data-driven workday.
“The data and simulation system processes we have cost a lot to create upfront,” McCann explains. “But they’re the right long-term solution, as we’ve already proven through the tech, we’ve been able to create even in the past few years.”
Many of the engineers that signed on to Intergalactic had proposed these ideas at their respective companies and were shut down. “They were sick of it,” McCann says. “These companies continue to use these outdated systems to create not-as-good products because they are a predictable money maker. When they heard how much R&D was required to produce systems that would cannibalize their existing cash cows that they’d been successfully producing for the last 50 years just fine, it was a pretty obvious no.”
It’s an issue with seeing the big picture, McCann thinks.
“That Joint Strike Fighter program is a trillion-dollar program, like the value of Apple in one military,” he says. “The same goes for the GBSD program that Northrop Grumman just signed––there’s lots of money swirling around our work. With that comes inherent, and understandable risk-aversion. Still, while it’s fair for the industry to be careful, they’re too cost-cautious, stripping programs to the bone, and making it impossible for engineers to do the work we need.”
McCann points to Boeing as an example. “After years of cost-cutting, Boeing is a shell of their old self, not innovating, facing tons of technical problems, and their engineers don’t like working there,” he says. “It’s sad to see, and why we adopted a culture of big picture thinking.”
In line with throwing caution to the wind, the Intergalactic team members took another risk: quitting those positions and working in southern Utah instead. “For many of us, it’s the best career decision we could have ever made. No one else in Utah, much less the country, is doing the work we’re doing,” McCann says.
Manuel, however, doesn’t see a trend of turning down new tech in aerospace. “We’re risk-averse because of what we do,” he agrees. “But I don’t connect those dots to a slowed-down industry––we’re just in a new age of tech. We’re not sending interoffice memos now, just like how we’re not doing the same testing we’ve done in the past.”
Regardless of the reason for the shift to data, both Utah-based companies are trailblazers, set to develop and mass-produce the fastest, most efficient jets we’ve ever seen in the shortest amount of time, and maybe even man a Mars flight or two.
Jacqueline Mumford
Jacqueline is a Master of Accounting student at the University of Utah. Specializing in tax, she's interested in business, government, and the intersection of the two. When she's not studying or writing, she loves to run, play Candy Crush, and read novels
(This article appeared in the August 2021 issue of Utah Business magazine. You can read the article on their site here: Space travel is closer than you think - Utah Business.)