How spaceship heat shields work
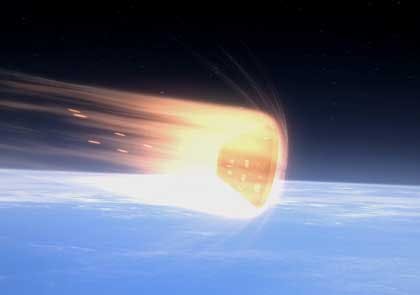
Blog
There’s a popular early-19th-century English phrase, “What goes up must come down,” that’s just as relevant today as it was 200 years ago. While fans of astronautics will state that ackchyually many solar-system and deep-space-exploration vehicles have been launched without the intent of their ever coming down, when it comes to human-piloted missions and particularly to the latest trends toward reusable space launch vehicles, one of the primary problems that must be solved is how to get people and spaceships back down to Earth safely.
To date, the only way that steely-eyed missile men and women have figured out how to do this is by using various types of heat shields on their reentry vehicles to prevent them from burning up in the Earth’s atmosphere. So, how do these heat shields work? Let’s see if we can shed some light on this *ahem* hot topic.
The problems of gravity and atmosphere
Objects approaching and entering (or reentering, in the case of spacecraft) Earth’s atmosphere are accelerated by Earth’s gravity while at the same time experiencing atmospheric drag or friction–which puts extreme mechanical stress on the object–and intense aerodynamic heating caused primarily by the shock/compression of the air in front of the fast-moving object, but also by drag as well. These forces can combine to cause a loss of mass (technically called “ablation”) or even complete disintegration of smaller, tougher objects–the results of which you can observe whenever you see a falling star–and objects with lower compressive strength can simply explode from the forces involved.
Projectiles like intercontinental ballistic missile warheads don’t have to be slowed for reentry, and are in fact designed in a streamlined way to maintain their hypervelocity (which is one reason they are so difficult to shoot down). However, reusable space vehicles, and of course any spacecraft with human passengers inside, must be slowed to below supersonic velocities before any parachutes or air brakes can be deployed or the vehicle can fire retrorockets for landing or recapture.
How fast are space vehicles moving during atmospheric reentry?
In a word, FAST. To date, successful reentry has been achieved with speeds ranging from 7.8 km/s (around 17,400 mph) from low Earth orbit (LEO) to around 12.5 km/s (just under 30,000 mph) in the case of the Stardust probe (Apollo 11 was moving at about 24,700 mph on its start of reentry, for reference). Since these vehicles have high kinetic energies and are greatly accelerated by Earth’s gravity, the only practical way of expending this energy is gradual slowing via atmospheric dissipation, which in effect converts velocity and kinetic energy into heat, necessitating the use of robust heat shielding.
You might ask why retrorockets couldn’t be used to slow the vehicle for a more gentle trip down through the atmosphere, but the forces involved are so great that it would be effectively impossible for a space vehicle to carry enough fuel to sufficiently slow it for reentry. Until nuclear space propulsion or antigravity engines become possible, heat shielding, and gradually slowing space vehicles via “friction” with the atmosphere, is the only practical way to complete the reentry procedure.
Ablative heat shields vs. refractory insulating heat shields
Over the decades of space launches and the development of reentry vehicles, multiple types of heat shielding for reentry have been tried, but there are two primary methods that have risen to the top and remain in use today: Ablative heat shields and refractory insulation tiles.
(Both of these fundamental approaches also necessarily require some application of “thermal soak” heat management or “passive cooling” in the design of the spacecraft, since inevitably some heat is transferred from the outer heat shield layer into the underlying structure, but in this article we’re focusing on the two main types of external heat shields.)
The term “ablation” refers to the removal or destruction of an object or part of an object by vaporization, chipping, or erosive processes, and that’s exactly what happens in an ablative heat shield. There have been multiple formulations and designs of ablative heat shields, including phenolic-impregnated carbon ablator (PICA), PICA-X, PICA-3, silicone-impregnated reusable ceramic ablator (SIRCA), and AVCOAT, all utilizing different constructions of carbon, silicone, resins, and/or epoxies, but all function in the same way. The science is extremely complicated and a true understanding involves a detailed knowledge of the various gas models in shock layer gas physics, but in very simple terms, an ablative heat shield consists of a layer of plastic resin, the outer surface of which is superheated to a gas, which then carries the heat of the compression/shock layer away by convection. An ablative heat shield functions as a sacrificial surface, creating a boundary layer utilizing the “blowing” of gaseous reaction products from the burning resins in the heat shield material, which lifts the hot shock layer gas away from the heat shield’s outer wall, creating a much cooler boundary layer as long as the temperatures and speeds are sufficient to maintain that gas barrier.
We’re talking about reentry vehicle surface temperatures of between 1477° C (2691° F) and 2900° C (around 5200° F, in the case of the Stardust reentry vehicle), so “cooler” is certainly a relative term.
Ablation occurs at two levels in an ablative heat shield: The outer surface of the ablative material burns, melts, and/or undergoes “sublimation,” or the process by which a solid may change directly into a gas without turning into a liquid first, while the majority of the ablative material undergoes “pyrolysis” (thermal/chemical decomposition in a high-heat inert or oxygen-free environment) and expels its product gases. The gaseous barrier produced by this pyrolysis is what creates “blowing” and helps block convective and catalytic heat transfer into the vehicle.
Interestingly, ablation can also provide protection against radiative heat flux if the formulation includes carbon and introduces it into the shock layer, making it optically opaque. Essentially, this can function like a big pair of sunglasses for the spacecraft. Pretty cool!
Ablative heat shields were used on the Mercury, Gemini, and Apollo spacecraft, and have been recently employed on the SpaceX Dragon 2 spacecraft as well as the Orion spacecraft. One interesting advantage of the ablative approach is that the material containing the resins can be somewhat flexible, as when used in inflatable heat shields.
The other primary approach to heat shielding on space vehicles employs refractory insulation, rather than ablation. A refractory-insulation type heat shield uses an extremely low-conducting outer material, commonly fabricated into smallish, replaceable tiles due to material strength constraints, combined with a heat-resistant base material, to keep the intense heat in the outermost layer of the spacecraft’s surface, where it is then conducted away by the air. The most well-known example is the black heat-shielding tiles covering the bottom surfaces and nose of the various Space Shuttles, the majority of which were constructed of high-grade quartz/silica (sand) fibers. These tiles reflect about 90 percent of the heat they’re exposed to back into the atmosphere, while the tiles’ interior and heat-resistant felt or ceramic wool underlayer absorbs the rest.
Since the surface temperature rises to incandescent (white-hot) levels, the refractory insulation material must necessarily have a very high melting point, while at the same time exhibiting very low thermal conductivity. Materials with these properties tend to be brittle, delicate, and difficult to fabricate in large sizes, so it’s for this reason that the refractory insulation layer is typically constructed from relatively small tiles that are then attached to the structural skin of the spacecraft using high-temperature adhesives or mechanical attachment points.
Engineers and designers have to walk a fine line here between material toughness and thermal conductivity. We can make materials that are extremely non-conductive, but these low-conductive materials are generally more brittle and fragile the less conductive they are. So, there’s a limit to the size and structural load-bearing capability of the material, which is why it’s almost always employed in small individual tiles. The Space Shuttle, with its complex curves, nose, and wing surfaces, needed literally thousands of individual tile shapes made, many of which would only fit in one specific spot on the Shuttle.
Modern “rapidly reusable” space launch and reentry vehicles are making use of less complex shapes, which allows the use of tiles of more uniform profiles and universal placement, such as the hexagonal tiles covering the “reentry” side of SpaceX’s forthcoming Starship. The nose portion and its tapering shape, along with the “fins,” utilize a similar, complex pattern of unique tiles to the Space Shuttles’, but the majority of the tubular, cylindrical surface can be tiled with mass-produced, identical pieces backed with ceramic wool insulation, all of which click into mechanical pins welded into the spacecraft’s skin. Here’s an excellent video detailing what we know so far about Starship’s heat tiles.
In many spacecraft/reentry vehicle designs utilizing this type of tiled heat shielding, the tiles will cover the great majority of the undersurface, with reinforced carbon-carbon heat sink material on the highest-heat-load points, such as the nose and any wing leading edges.
You might wonder why reentry vehicles have wide, flat, and/or gently rounded surfaces, rather than “aerodynamic” or pointy shapes, which you could argue might reduce drag, and thus heat, upon reentry. Well, studies show that, in effect, the “pointier” an object is, the closer the high-speed compression shockwave barrier–and the heat resulting from that compression–will be to the surface of the vehicle. The wider and flatter the object, the larger the “cushion” between the leading edge of the vehicle and the shockwave barrier, and the lower the heat load that has to be dealt with. This is why the Apollo space capsules, the Space Shuttle, and even upcoming vehicles like SpaceX’s Starship have large, wide, rounded surfaces where they meet the atmosphere on reentry.
What happens when heat shields fail?
Rocket scientists are pretty frickin’ smart, but like all scientists, they sometimes get it wrong, and sometimes the only way we can learn is by making mistakes. At times the data modeling used to make assumptions and designs is wrong, and occasionally the methods, materials, or construction are proven ineffective. The results of both kinds of errors can be disastrous, and even fatal.
These errors may be failures or inaccuracies in analysis, as in one example where, “Both the Apollo command module and the Space Shuttle were designed using incorrect pitching moments determined through inaccurate real-gas modelling. The Apollo-CM’s trim-angle angle of attack was higher than originally estimated, resulting in a narrower lunar return entry corridor. The actual aerodynamic center of the Columbia was upstream from the calculated value due to real-gas effects. On Columbia’s maiden flight (STS-1), astronauts John Young and Robert Crippen had some anxious moments during reentry when there was concern about losing control of the vehicle.”
On the other hand, an error may be the failure to fully consider the effects of the launch or flight environment, as in the case of the 2003 Columbia disaster, where foam debris from part of a structure that attached the external fuel tank to the shuttle appeared to strike Columbia’s left wing after liftoff. It was later found that a resulting hole on the left wing allowed atmospheric gases to bleed into the shuttle as it went through reentry, and the spacecraft disintegrated, killing all 7 astronauts aboard, and leading to the eventual retirement of the Space Shuttle fleet.
In the case of the Space Shuttle, each craft was covered by around 24,000 refractory heat-shield tiles, and the Smithsonian reports that each tile was meticulously and laboriously inspected before each flight, with between 30 and 100 tiles needing to be replaced before each mission (and as noted above, each had to be custom-made specifically for its unique place on the Shuttle). It remains to be seen whether innovative, rapidly replaceable heat shield designs like that of SpaceX’s Starship can live up to their design potential, but if they prove economically and practically feasible, they may greatly accelerate the “refit” process, transforming how humans and technology go up to space and come down safely.
–By Jeff Davis, Intergalactic Scribe
Sources:
https://southernresearch.org/helping-apollo-spacecraft-beat-fiery-re-entry/
https://www.nasa.gov/directorates/spacetech/game_changing_development/HIAD/irve3-success.html
https://www.daviddarling.info/encyclopedia/R/reentry_thermal_protection.html
https://www.smithsonianmag.com/air-space-magazine/shuttle-tiles-12580671/
https://www.space.com/19436-columbia-disaster.html