2022-02-14
Microtube heat exchangers are changing the game in aerospace thermal management
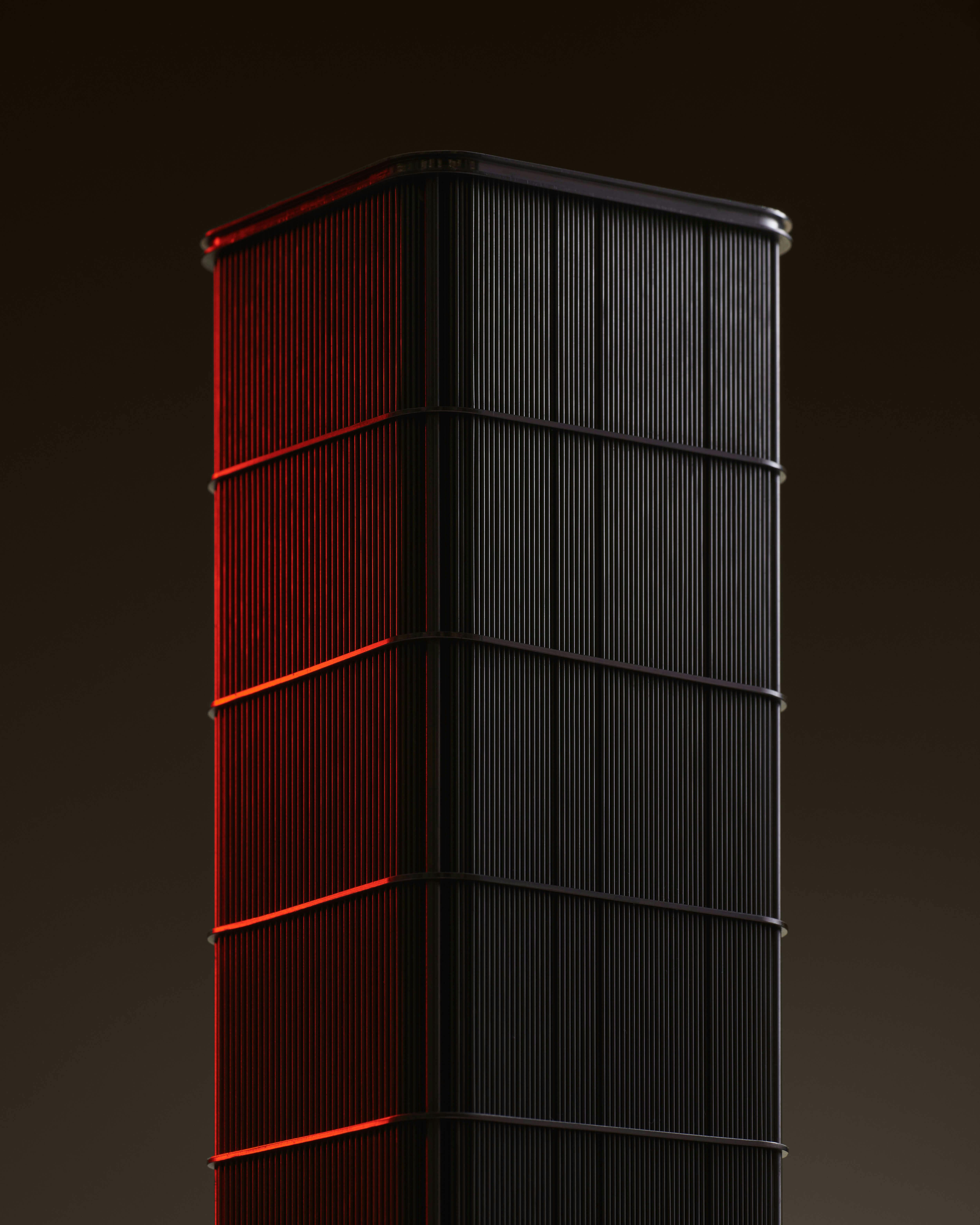
Blog
You probably woke up this morning with this burning question running through your febrile mind: “What is a heat exchanger?” Well, today’s your lucky day! Heat exchangers are actually *ahem* really cool. And as it happens, managing heat—specifically heat rejection—is absolutely integral to all types of aerospace applications. So let’s go over some basics, and then we’ll talk about why Intergalactic’s patent-pending microtube heat exchanger designs are allowing advances in aerospace that were previously thought impossible.
What is a heat exchanger and what are some common types?
In very simple terms, a heat exchanger is a device or system used to transfer heat between two or more fluids, including liquids, gases, and air. They are very versatile and can be used in both heating and cooling applications. Heat exchangers are used in multiple industries, including industrial heating and cooling, chemical plants, power stations, refineries, and many others, including aerospace, aviation, and land/sea vehicle applications.
The double-pipe heat exchanger
The simplest type of heat exchanger used in industry, and probably the simplest to describe to someone, is a double-pipe heat exchanger, sometimes called “pipe-in-pipe.” In very basic terms one (usually horizontal) pipe is fitted inside a larger pipe, with enough space around the inner pipe that fluid can flow around it. One fluid is pumped through the inner pipe, and another is pumped around it, inside the outer pipe, and the heat of one fluid transfers through the walls of the inner pipe to the fluid flowing around it, or vice versa.
This type of heat exchanger is often used under severe fouling conditions (when one or both of the fluids is full of contaminants or debris) because of the ease of cleaning and maintenance. It also allows very high flow rates due to the large diameters of the pipes .The major disadvantages to the double-pipe heat exchanger are that it is heavy, bulky, and relatively expensive considering its inefficient “per unit” heat transfer capability compared to more advanced designs.
The shell-and-tube heat exchanger
A related type of heat exchanger that evolved from the double-pipe design is the shell-and-tube or “shell tube” type heat exchanger. The concept is similar to the simple double-pipe heat exchanger, but rather than a single internal pipe, the shell and tube design features a large outer pipe or “shell” (typically welded steel) that contains multiple inner pipes or “tubes” (even dozens), rather than just one. Additionally, the flow of the “outer” fluid is directed across the inner tubes multiple times by a system of vertical baffles that also increase fluid turbulence and heat transfer efficiency compared to a simple pipe-in-pipe arrangement.
The shell-and-tube exchanger is one of the most popular types for many industries due to its relatively low cost, and its flexibility in handling a wide range of pressures and temperatures. A disadvantage of this type of heat exchanger is susceptibility to internal or external corrosion, as well as internal blockages due to fouling if the fluid flow is not turbulent enough. However, the main issue with the shell-and-tube design is its size and weight which typically restricts this heat exchanger type to industrial, land based applications.
The plate-fin heat exchanger
The plate-fin heat exchanger is an optimized, efficient type of the plate heat exchanger, sometimes called “plate in frame” depending on design and application. Rather than any variation of inner and outer pipes or tubes, the plate-fin heat exchanger consists of multiple layers of corrugated metal sheets compressed by flat metal plates to create a series of thin, finned chambers. Separate hot and cold fluid streams flow through alternating layers of the heat exchanger.
The entry and exit ports and the flow of the different fluids are typically defined by carefully alternating gasket surfaces that prevent the fluids from mixing when the sheets are clamped together between the outer plates like a big, hot, juicy metal sammitch.
Key advantages of the plate-fin type of heat exchanger are its efficiency compared to the tube types discussed above, its compact size (though this is relative as we will see below), and depending on the design, you can add or remove sheets between the plates to suit a particular application, so it’s fairly versatile.
The plate-fin heat exchanger can be about 5 times lighter in weight than that of a shell and tube heat exchanger when comparing roughly equivalent heat-transfer performance. This is why the plate-fin heat exchanger has become common workhorse and is ubiquitous in legacy aerospace applications.
One disadvantage of the plate-fin heat exchanger is that the small passages can quickly become clogged or fouled, particularly if it is exposed to ambient conditions with risk of Foreign Object Debris (FOD). One source says the maximum service life without cleaning is ~3 years.
For our visual learners, here are a couple good video/animation explanations and exploded diagrams of plate-fin heat exchangers and shell-and-tube heat exchangers.
Microtube heat exchangers are a giant leap forward in aerospace thermal management technology
Since the mid-2010s, Intergalactic has been pioneering, perfecting, and patenting a new type of heat exchanger using proprietary microtube technology. Microtube heat exchangers have been used in some edge cases, like Formula One racing, but were typically seen as future tech in aerospace until we got serious about refining and commercializing it for airborne applications.
In basic terms, Intergalactic’s microtube heat exchanger designs enables performance that goes beyond what today’s conventional shell/tube or plate-fin designs can do simply by maximizing heat transfer surface area in a given volume, resulting in smaller size and weight, higher heat rejection capacity, and nearly limitless form factor flexibility. Here are the three main areas where microtube heat exchangers are changing what is possible in aerospace applications:
1. Drastic reductions in size and weight
Keeping weight and size to a minimum is an obsessive, primary pursuit in aerospace. On a Nimitz-class aircraft carrier that weighs around 99,000,000 kilograms (218 million pounds), a large, heavy, conventional shell-and-tube or plate-fin heat exchanger may be entirely appropriate. However, in the tight confines of an aircraft or spacecraft, where literally every gram of weight and cubic centimeter of space is examined, re-examined, scrutinized, and prioritized, the microtube heat exchanger’s advantages become obvious.
Intergalactic’s microtube tech results in best-in-industry heat rejection per weight and volume, with world-class size, weight, and pressure drop characteristics compared to traditional, brazed plate-fin technology. Bottom line? Microtube technology allows you to reduce the size and weight by a factor of ~3 for the same pressure drop and heat transfer performance, or choose to achieve 3X the heat rejection capability while staying in the same size and weight envelope. In real-world aerospace applications, Intergalactic has seen upwards of 50%-80% reduction in weight and/or volume for microtube heat exchangers compared to conventional heat exchanger technology. Money.
2. Nearly infinite flexibility in form factor and application
Legacy brazed-plate fin has been the default heat-exchanger technology for decades, but its size and shape limitations make it a tough sell on many modern programs. Microtube technology allows nearly infinite flexibility in form factor, which matters when you need to fit heat rejection systems into small or awkwardly shaped spaces.
Intergalactic has designed and tested microtube heat exchangers for a number of different working fluid applications including refrigerants, air, and liquid coolants such as polyalphaolefin (PAO), propylene glycol (PGW), ethylene glycol (EGW), as well as ocean salt water. Working pressures for different tested microtube heat exchangers have ranged from as low as a few psi at high altitude ambient air pressure to as high as tens of thousands of psi in deep undersea applications. Working temperatures can go well below freezing to as high as hundreds of degrees Celsius, depending on the application.
This flexibility allows diverse microtube applications in aerospace, aviation, land and sea vehicles, and even directed energy systems.
3. Reliability, durability, and redundancy
Microtube heat exchangers pack hundreds to upwards of tens of thousands of small, syringe-needle-sized tubes into an array, which provides extremely efficient heat rejection and durability along with redundancy. You can lose some tubes to damage or fouling and keep right on shedding heat effectively (not that this happens often since our tubes are made of stable and resilient stainless steel or other high performance alloys).
Why “legacy” military and commercial aerospace heat exchangers are limited when reducing size and weight
Conventional shell-and-tube heat exchangers typically have tube diameters of around 0.25 to 0.5 inches (~6 to ~13mm). These tube diameters are similar in scale to conventional plate-fin heat exchanger channel heights, which typically range between 0.1 and 0.5 inches.
Plate-fin type heat exchangers are often described as “compact” heat exchangers because, compared to the shell tube type, they are much smaller in size and weight. However, attempts to design plate-fin exchangers with channel heights much smaller than 0.1 inches typically result in difficulty handling and correctly stacking the fins and plates during assembly. This limitation fundamentally restricts how much heat transfer surface area can be packed into a given fixed volume using this conventional technology.
Plate-fin heat exchangers are also susceptible to fouling which can significantly reduce or even block the flow of heating/cooling fluid, and this effect gets worse the smaller you go.
At Intergalactic, we’ve developed proprietary technology that allows us to build microtube heat exchangers with tube diameters down to 0.02 inches… that’s significantly smaller than your conventional shell and tube or plate fin heat exchanger. And since we can pack tens of thousands of tubes into an array, that means more direct primary heat transfer surface area to exchange heat between the fluid streams … like a LOT more, theoretically ~7 to ~25 times more in fact!
More advantages of microtube heat exchangers compared to conventional plate-fin designs
Designers of plate-fin heat exchangers often attempt to increase heat transfer performance by adding “secondary” heat transfer area in the form of additional fins. While this may add some additional surface area for heat transfer, it also comes with two gotchas.
First, this secondary finned area is less effective than the primary area because the fins are not as efficient as the direct primary area because of the additional resistance encountered when first conducting heat from the fin to the primary surface area of the plates. Second, this inherent inefficiency often results in a larger, heavier heat exchanger unit as compared to a microtube heat exchanger that is capable of the same heat transfer performance.
With a microtube system, all the additional surface area for the microtube heat exchanger functions as primary heat exchanger surface area, meaning that both fluids are in direct contact with the heat exchanger material (the tube walls).
Effectively, this means that a microtube heat exchanger can be many times more efficient than a conventional plate-fin heat exchanger for the same weight and size.
Conventional plate fin heat exchangers often employ brazing to join the fins and plates together. That process can be inconsistent, and the quality is highly dependent on the brazing method. The brazing operation can also require a process step to remove the oxides that are built up during the brazing, and may require subjecting the heat exchanger to “pickling solutions” that often contain acids to eat away the oxides that are produced.
Conversely, Intergalactic employs a proprietary laser-welding process to join the microtubes to the heat exchanger end plates, resulting in a simpler and cleaner manufacturing process and a more mechanically robust product.
In addition to stainless steel, we’ve been developing microtube heat exchangers in Inconel and other high-performance alloys for space applications.
For every new design, Intergalactic will launch their optimization algorithms to generate the best heat exchanger design specific to what’s most important in your particular application. Be it weight, performance, volume, cost, or complexity, Intergalactic can show you how these different parameters trade and help guide you to the best design for your specific platform. Its optimization engine is all built on the back bone of the proprietary physics-based models we’ve built in house and validated through testing in our wind tunnel lab, our team of heat transfer engineers, and Intergalactic’s Model Based Design philosophy.
Additive vs. laser-welded microtube heat exchanger construction
An emerging technology that is gaining ground in heat exchanger manufacturing is additive construction, or 3D-printing. While Intergalactic is equipped for additive modeling and construction if that is what the client specifies, let’s go over some points of comparison between the two.
First, while additive manufacturing can result in heat exchangers that are more efficient and lighter than plate-fin, microtube technology is even more efficient and lighter than what additive can currently provide today.
Additive construction results in materials that are brittle by nature, with unpredictable pits and stress-risers, and are vulnerable to debris flaking or breaking off internal finish surfaces. Wall thicknesses for today’s additive heat exchangers are also significantly thicker than for microtubes owing to limitations during today’s additive capabilities for producing thin walls without causing leaks between streams. Surface finish on additive surfaces can sometimes also be complicated as it is typically rougher for the additively manufactured which causes higher pressure drop. Laser-welded microtubes are made of durable and corrosion-resistant stainless steel, with options for Iconell or Ionell alloys if desired.
With an additive design, leaks can potentially occur anywhere and there’s no possible internal inspection method. With the laser-welded microtube construction, the process includes microscopic weld inspection at the only localized area for potential leaks.
Finally, the initial buy-in for additive manufacturing is steep, at around $1 million per machine. On the other hand, there’s no buy-in for Intergalactic’s proprietary microtube technology. It’s order, grab, and go.
So, now you know a bit more about heat exchangers. Aren’t they awesome?
Learn more about our Boreas3 Heat Exchanger and get in touch if you want to talk shop.
- Jeff Davis, Intergalactic Scribe, with contributions from Thermal Magi Tony Ho and Nick Kaiser
Sources:
https://iopscience.iop.org/article/10.1088/1757-899X/963/1/012027/pdf
https://www.thermopedia.com/content/1121/
https://en.wikipedia.org/wiki/Heat_exchanger
https://en.wikipedia.org/wiki/Plate_fin_heat_exchanger
https://en.wikipedia.org/wiki/Plate_heat_exchanger
How Shell and Tube Heat Exchangers Work (Engineering) https://youtu.be/OyQ3SaU4KKU
Plate Heat Exchanger: How it works https://youtu.be/br3gkrXTmdY