De Havilland Comet: the rocky history of the first commercial jetliner
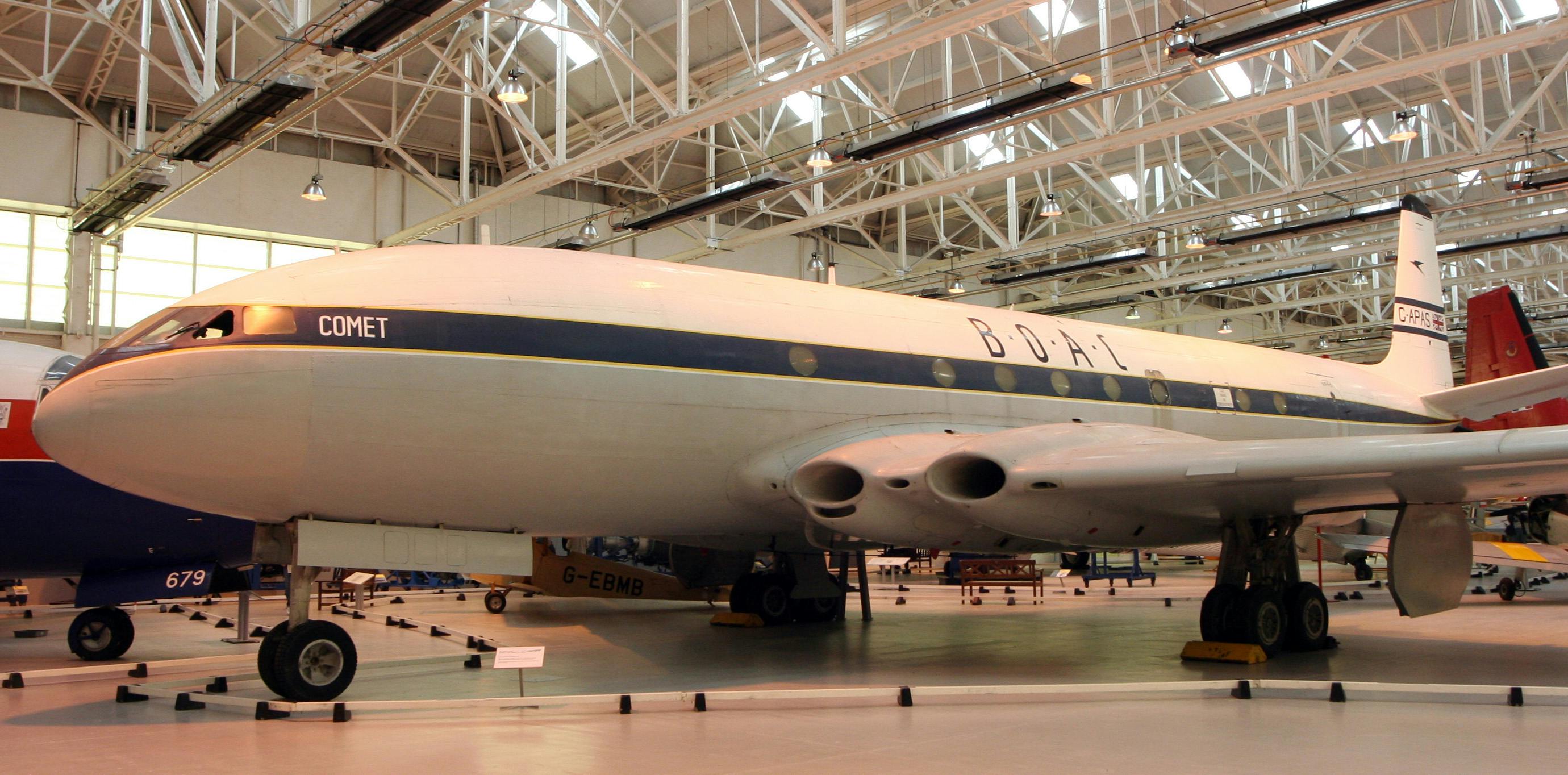
Blog
Today, seeing the white contrails of jetliners criss-crossing the sky is as common as seeing drivers texting, but this wasn’t always the case. Jet airliners were the stuff of fantasy until the 1950s. As often happens throughout the history of powered human flight, the militaries of the world were the first to fully embrace and develop the new concept of using jet engines to power aircraft. There were two notable jet fighters used in WWII, namely the Messerschmitt Me 262 (first flown in combat by the Germans in July 1944) and the Gloster Meteor (first flown in combat missions on the continent by the British in January 1945), though both were fielded late in the war and never faced each other in a dogfight. However, though it was clear early on that jet-powered aircraft were the way forward for the military, in commercial aviation it took a while longer for the concept to catch on, and the first attempts proved to be pretty rocky.
Let’s take a look at the first commercial jet airliner and some of the hard, painful lessons it taught the world of aviation.
The de Havilland DH.106 Comet was a groundbreaking design
Initial testing of jet engines for military transport aircraft and potential commercial use was undertaken using “legacy” propeller-driven airframes and swapping out the piston engines for turbojets. Though they were fairly clunky, even these early conversions showed dramatic reductions in noise and vibration for the passengers. Wing Commander Maurice A. Smith, winner of the Distinguished Flying Cross for his excellent service flying bombers during WWII said, “Piloting a jet aircraft has confirmed one opinion I had formed after flying as a passenger in the [early] jet test beds, that few, if any, having flown in a jet-propelled transport, will wish to revert to the noise, vibration and attendant fatigue of an airscrew-propelled piston-engined aircraft.”
As jet engine performance improved throughout the 1940s, range increased to the point where jet aircraft could be considered as practical replacements for prop-driven airliners. A request by the British Brabazon Committee asked for the post-war development of a hull-pressurized mailplane capable of carrying 1 long ton (2,200 lb/1,000 kg) of payload at a cruising speed of 400 mph (640 kph) non-stop across the Atlantic. The majority of aircraft designers felt that jet engines were too inefficient and unreliable for the task, but Sir Geoffrey de Havilland, head of the de Havilland aircraft company, foresaw the potential of the new technology and insisted on his company’s proposal for a fully turbojet-powered aircraft that would meet this need.
De Havilland was awarded a development and production contract in 1945 for the “type 106,” and over the next few months the concept morphed from a mail-carrier with as few as 6 seats to a long-range airliner with 24 seats and a proposed cruising altitude of 40,000 feet. The initial proposals were so attractive that the British Overseas Airways Corporation (BOAC) submitted orders for 10 aircraft by the end of 1945.
One of the early roadblocks faced by de Havilland was that there were no turbojet engine manufacturers in the world that were working on design specs for an engine with the power and fuel consumption requirements to achieve de Havilland’s goals. This meant that de Havilland had to take the lead on both the development of the airframe and the engines, which is a tall order when we’re talking about a completely new concept in aviation.
Chief designer Ronald Bishop tried several funky airframe layouts, including canard-wing, flying wing, and tailless designs, but in 1946 BOAC requests and de Havilland’s practicality convinced Bishop to settle on an expanded 36-passenger (4 abreast with a central aisle) design with a 20-degree swept wing and an unswept conventional tail section, and the aircraft was designated the DH.106 Comet in December 1947.
The airliner had 4 turbojet engines incorporated into its wing roots near the fuselage, 2 on each side. The result was a gorgeous airplane with streamlined air intakes and organic-looking engine/wing nacelles, though this layout necessitated heavier structural wing bracing near the fuselage and made it a little more difficult to service the engines compared to later airline designs such as the Boeing 707 with its 4 engines hanging from in separate, under-wing mounts (like all jetliners today). Additionally, heavy armor plating had to be added around the engines to protect passengers in the case of engine failure and debris. The engines included baffles to reduce noise emissions to the outside world, and extensive soundproofing was used in the fuselage to reduce passenger fatigue.
Advantages of this engine layout went beyond aesthetics, however. Bishop elected to move forward with the embedded-engine configuration because it avoided the drag of podded engines, and also meant that the stabilizer fins and rudders could be smaller with the engines’ thrust concentrated closer to the centerline of the fuselage. Additionally, placing the engines within the wings and close to the fuselage reduces the risk of foreign object damage such as bird strikes, which can seriously damage jet engines.
When this kind of innovation is taking place, all aspects of an aircraft’s development and testing can be impacted. The desire for a fully pressurized cabin was a key factor in the design, and this alone became a large issue. Though the Boeing 307 Stratoliner prop-driven airliner had a pressurized cabin in 1938 and flew at 20,000 feet, the proposed altitude of the new “jetliner” was double that. Maintaining large pressure-testing chambers suitable for accurate durability/fatigue testing proved impractical, so de Havilland developed an underwater system where pressure conditions could be simulated more easily and failure points more accurately tracked.
More innovations included powered controls to alleviate pilot fatigue and prevent aerodynamic control reversal (possible in some conditions), quadruple-redundant hydraulics, geared elevators to prevent overstressing the airframe (a concern when using power controls), and an entirely new advanced alloy-composite skin that was both riveted and chemically bonded using a new adhesive, which saved weight and reduced the risk of fatigue cracks spreading from the rivets. The new composite/alloy fuselage and wings also had the advantage of simplifying the manufacturing process.
The first Comet prototype flew in July 1949, and the second a year later. The prototypes were thoroughly tested by BOAC in route-proving and crew-training throughout 1950 and 1951. Production Comets began flying in May 1952, and the modern jetliner era was born. The Comet could carry its passengers up to 2,500 miles (4,000 km) at a cruising speed of 450 mph (720 kph) at a normal service ceiling of 36,000 feet (11,000 meters). The impact of bad weather was greatly lessened at these altitudes, and passengers initially were treated to luxury amenities such as reclining “slumberseats” with 45 in (1,100 mm) centers for ample leg room, stunning views through the Comet’s large, square passenger windows (more on these later), and table seating accommodations. Passengers could enjoy hot and cold food and drinks, a bar, and separate men’s and women’s toilets. Ah, the good old days of air travel. This honeymoon phase of the jetliner era wouldn’t last long, however.
Early hull losses (crashes) and lessons learned from the de Havilland Comet
Unfortunately, history shows that innovation in aerospace often comes at a heavy price, and fatal accidents are sometimes the impetus that leads to learning. The first indication that there may have been a problem with the new DH.106 Comet jetliner was on October 26, 1952, when a BOAC Comet failed to become airborne from Rome’s Ciampino airport and ran into rough ground at the end of the runway. There were no fatalities, but two passengers sustained minor injuries. The aircraft, however, was a total loss. Then, on March 3, 1953, a Canadian Pacific Airlines Comet failed to become airborne when departing the Karachi, Pakistan airport, plunged into a dry canal and smashed into the embankment, killing all 5 crew and 6 passengers on board. This was the first fatal jetliner crash in history. In response, Canadian Pacific canceled its remaining orders for Comets and never flew the type again.
Both of these early Comet accidents were originally attributed to pilot error, citing over-rotation (too-aggressive nose lift at takeoff) that led to a loss of lift from the wings’ leading edges. Further investigation showed that Comet’s original wing profile caused a loss of lift at a high angle of attack, and this was worsened by a lack of pressure recovery caused by the shape of the engine inlets under the same high angles of attack. As a result, de Havilland re-profiled the Comet’s wings’ leading edges with a pronounced “droop” to alleviate this loss of lift, and wing fences were added to control lateral air flow. The engine inlets were eventually reshaped and enlarged as well in later variants.
Another Comet hull loss occurred on May 2, 1953, when an aircraft departed from Calcutta, India, but crashed in a severe thunderstorm 6 minutes later, killing all 43 on board. Witnesses reported the aircraft was falling, on fire, and without wings before it hit the ground, which led crash investigators to suspect structural failure. This incident was blamed on pilot error overstressing the airframe in heavy weather using the fully powered controls. It was determined that the pilot may have overcorrected and caused an extreme negative-G condition on the wings in a dive, shearing them off. Metal fatigue was still not considered as a cause of the failure, and was not widely understood at the time. As a result of this fatal crash and investigation, future Comets were equipped both with weather radar and an innovative “Q feel” control system that helped transmit proportional feel to the pilot via the power controls.
Unfortunately the Comet was still flying with undiagnosed metal fatigue problems, and on January 10, 1954, BOAC flight 781 (which was the first production Comet in service) broke up 20 minutes after departing from Rome’s Ciampino airport (yep, Rome again) and crashed into the Mediterranean, killing all 35 people aboard. Engineers and investigators were baffled as to the possible cause, and BOAC voluntarily grounded its Comet fleet until a reason could be identified.
An investigative committee fielded theories from sabotage to window failure to fuel tank fire (to, we’re guessing, aliens), and the Royal Navy began recovery and forensic investigation of the airframe. However, pressure from the British government and BOAC may have influenced the committee to conclude that there was no apparent fault in the aircraft, even before the aircraft recovery process had been completed and forensic examination could be performed. The Comet fleet was returned to service in March 1954.
Sound a little premature? It was. Only 2 weeks later on April 8, 1954, another Comet crashed into the Mediterranean (after taking off from, guess where? Rome) with the loss of all 21 passengers and crew on board. The Comet fleet was immediately grounded (again), its Certificate of Airworthiness was revoked, and Comet 1 line production was suspended while an investigative group was formed. Prime Minister Winston Churchill (he served twice, remember) tasked the Royal Navy with helping locate and retrieve the wreckage so that the cause of the accident could be determined.
In October 1954 the Cohen Committee Court of Inquiry was formed to investigate and determine the cause of the Comet’s fatal crashes. Eventually a complete pressurized fuselage was placed into a water tank and subjected to repeated pressurization/decompression cycles, which exposed some key flaws. The fuselage ripped open at a bolt hole and the skin was too thin—and the fuselage supports too weak—to prevent the failure from spreading. The investigators repeated the test and got similar results.
Based on these findings, the investigators examined recovered parts of the crashed Comet and found fatigue cracks that had grown around improperly riveted holes near the cutout for the Automatic Direction Finder (ADF) instrument, resulting in explosive decompression of the fuselage. It was also found that the punch-rivet construction technique employed in the Comet’s design had exacerbated its structural fatigue problems. The Comet’s windows had been engineered to be glued and riveted, but had been punch-riveted only (rather than properly drill-riveted). Imperfections around punch-riveted holes could cause stress risers and fatigue cracks could start developing around the rivet, which was worsened by the too-thin fuselage skin of the original Comet. This finding, along with the press’s misreading of the term “window” (cutout) around the ADF, led to widespread rumors that the square passenger windows of the Comet were the cause of metal fatigue and decompression, and this old wives’ tale in commercial aviation continues to this day.
As a result of the Cohen Committee’s determination that the basic aircraft design was sound, but that it required improvements in materials and construction methods, the Comet was improved and resumed service in 1958. The Comet 2 was updated with thicker fuselage skin, better wing supports, round-edged windows (without a real reason for doing this), and other upgrades, and the revised Comet 2, 3, and 4 continued in service until 1997 with some airlines, though the highly publicized early crashes certainly left somewhat of a stain on the aircraft’s reputation.
Optimists will point out that the Comet’s troubled beginnings eventually led to multiple life-saving advances in both aircraft design and modern airline accident investigations. It’s tragic that often these types of learnings only come at the price of innocent lives.
–By Jeff Davis, Intergalactic Scribe
Sources:
https://www.history.com/this-day-in-history/first-jet-makes-test-flight
https://www.rafmuseum.org.uk/research/archive-exhibitions/comet-the-worlds-first-jet-airliner/
http://thetartanterror15.blogspot.com/2012/05/wcdr-maurice-smith-dfc.html