Your ultimate guide to next-gen space materials: superalloys and advanced composites
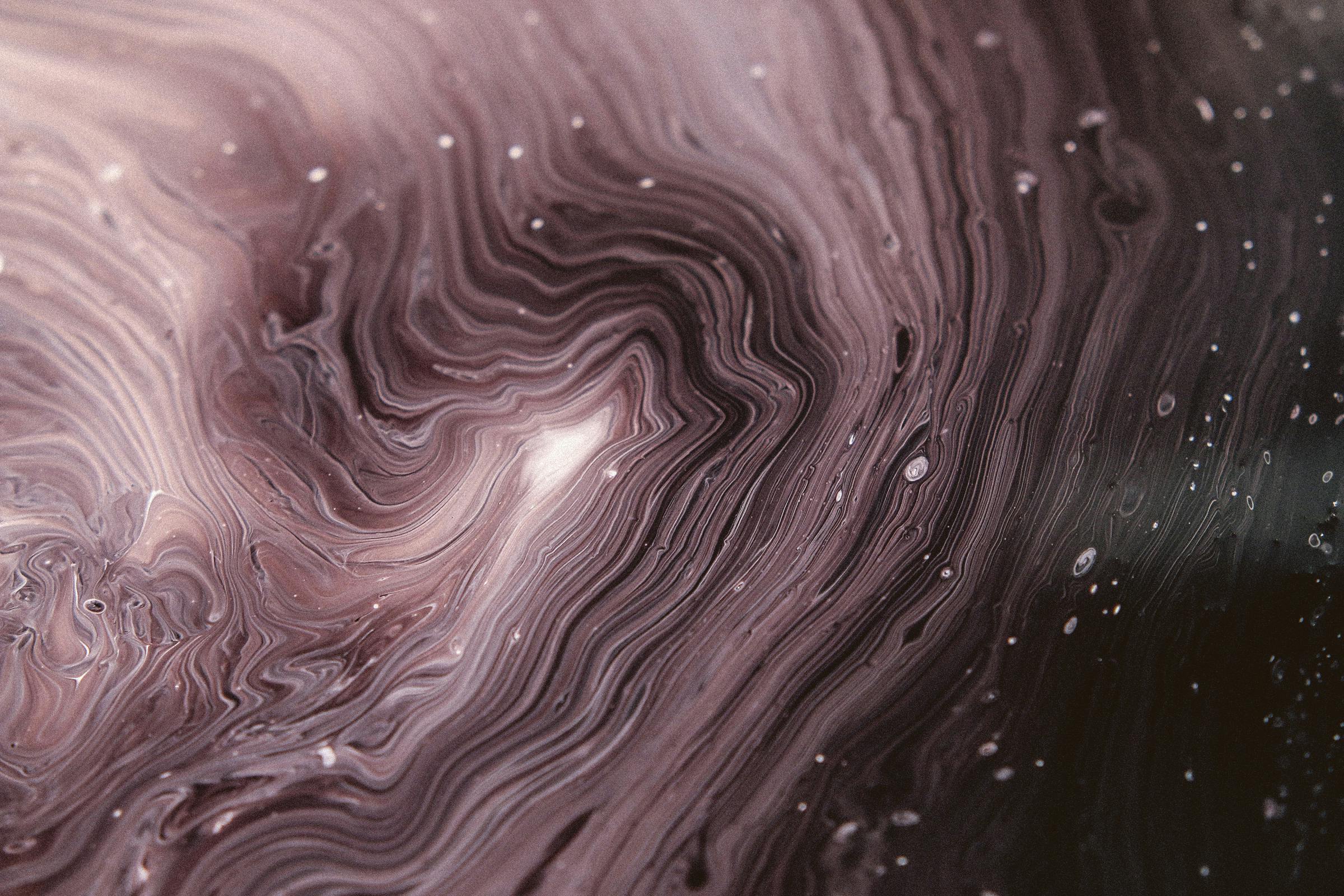
Blog
When you hear the term “space-age” referring to technology, materials, or techniques, you can be sure it refers to the cutting edge of human endeavor and scientific advancement. While the space age technically began over 65 years ago with the launch of Sputnik 1 in 1957, the term still connotes the frontier of research, development, design, and engineering. So when someone starts talking about “next-gen” space or aerospace materials, you know they don’t mean bailing twine and reclaimed barn wood.
It might seem like our postmodern age has reached the pinnacle of materials science and technology, but out-of-the-box thinkers and scientists continue to explore new avenues of learning and experimentation, developing methods, compounds, and materials that are pushing the envelope of even the best-performing aerospace materials to achieve what was thought impossible before.
We’re going to give you an overview of some of the next-gen materials being used in the modern space economy, including superalloys and advanced composites, and show you how they just might change the world.
What are superalloys and why are they essential for aerospace?
Time was, aluminum was cutting-edge aviation technology, used in the Zeppelin airships and notably in the engine of the first successful airplane, the Wright Flyer in 1903. This lightweight metal helped make powered human flight possible, and is still essential in most aircraft to this day. However, in the rocket and jet age, aluminum and even stainless steels would prove inadequate for heat and stress of modern designs, and engineers began to develop superalloys that were light, strong, and resistant to heat and oxidation.
A full and detailed understanding of superalloys would require advanced degrees in metallurgy and engineering, but in general terms, a superalloy is a metal alloy capable of extraordinary mechanical strength, corrosion resistance, heat resistance, thermal creep deformation resistance, and surface stability. Most superalloys used in aerospace today use nickel (Ni) as a primary component.
The term “super-alloy” or “superalloy” was first used just after the end of World War II, when aircraft turbine engines were in their first generation of development, and a select group of high-performance alloys proved suitable for use in the extremely high temperatures produced by these engines. So, while some of these alloys had been developed as early as the 1930s for use in seawater piping, steam fittings, and other high-demand applications, the term “superalloy” is fundamentally an aerospace term, though the alloys that were later developed specifically for aviation and space vehicles have since found a home in many other industries, such as chemical processing plants, computing, HVAC systems, and automotive applications.
The primary attributes of a superalloy where aerospace is concerned are their ability to retain strength and structural integrity even after lengthy periods of exposure to temperatures above 650°C (1,200°F), which naturally is important when building rocket motors, exhaust nozzles, jet turbine fans, high-heat/high-pressure valves, and more. Also key is their low-temperature ductility and surface stability, as well as remarkable corrosion resistance. Since superalloys also exhibit high strength-to-weight ratios, they are ideal for the high-temperature, high-pressure, low-mass requirements of aerospace applications. Let’s go over a few of the biggies, along with some recent breakthroughs.
Inconel
Probably the most well-known of all the superalloys, Inconel is now an entire family of alloys that include not less than 42% and up to 70% nickel, with significant chromium and iron levels. The many Inconel variants – tweaked to meet specific operational requirements – include small additions of aluminum, niobium, molybdenum, titanium, aluminum, and/or cobalt. The primary advantage of Inconel is that it is extremely resistant to oxidation and corrosion due to high pressure and heat. When exposed to high temperatures, Inconel forms a thick, stable, oxide-coated layer that protects the surface from further oxidation and decay. This type of performance is vital in jet engines and rocket motors.
The nickel-based Inconel superalloys became famous for their ability to remain operational at 90% of their melting temperature while withstanding high mechanical stresses in harsh environments.
Interestingly, though some of the early Inconel alloys were indeed employed in jet engines in the 1940s, Inconel 625 (one of the most widely used variants) was initially developed for use in ultra-critical steam-line piping. However, Inconel has been widely used in seawater, aerospace, and chemical processing applications, and has recently become commonplace in high-tech, high-heat automotive use such as in Tesla’s Model S main battery pack contactor, Ford’s turbocharger turbine wheels and valves, and BMW’s exhaust manifolds.
Because of its toughness and heat-shedding properties, Inconel is a difficult metal to shape and machine using traditional milling or cold forming techniques. This is partially due to the metal’s tendency toward rapid work hardening. After a single pass with a machine tool on Inconel, work hardening tends to plastically deform either the Inconel workpiece or the tool on subsequent passes. For this reason, designers and engineers utilizing age-hardened alloys such as Inconel 718 typically specify machining using an aggressive, but slow cut with a hard tool, which helps minimize the passes required.
Due to the material’s toughness and fondness for dulling or destroying mechanical blades and cutters, water-jet or laser cutting and grinding is the preferred method for forming many Inconel alloy components to final shape and finish, though Inconel can be carefully welded using gas tungsten arc welding or electron-beam welding techniques, and certain varieties may even be “3D printed” using today’s advanced additive manufacturing.
Inconel has been used in practically every important aerospace application over the past 70+ years, in fact, according to one study, Inconel 718 makes up more than 30 percent of a modern aircraft engine’s finished component mass. But here are just a few other notable uses of Inconel superalloys:
- The Space Shuttle’s studs securing the solid rocket boosters to the launch platform
- The external skin of the North American X-15
- Rocketdyne’s thrust chamber tube bundle, reinforcing bands, and manifold of the F-1 rocket engine used in the first stage of the Saturn V booster
- SpaceX’s Merlin engine manifold powering the Falcon 9 launch vehicle
- SpaceX’s SuperDraco rocket engine combustion chamber providing the launch escape system for the Dragon V2 crew-carrying space capsule (fully 3D printed from Inconel using a process of direct metal laser sintering)
- SpaceX’s Raptor rocket engine manifolds, cast from SX300 (later SX500) monocrystal nickel alloys (improvements over older Inconel alloys)
- Innumerable applications in jet aircraft tailpipes, vector nozzles, and many other components
One source sums up the extremely valuable, temperature-flexible properties of Inconel thus: “Jet engines present unique challenges for design engineers, as they are subject to extreme temperatures at both ends of the scale. At cruising altitude, the average outside air temperature is about -56.3°C (-74.7°F), while the actual combustion process can exceed temperatures of 1,150°C (2,120°F).”
There are other reasonably well-known and widely used nickel-based superalloys such as Waspaloy (an alloy of nickel, cobalt, chromium, and molybdenum), NIMONIC (typically consisting of more than 50% nickel and 20% chromium with additives such as titanium and aluminum), and the Haynes/Hastelloy family of superalloys, all of which have found extensive use in aviation and aerospace. Truly, the Ni-based superalloys are aerospace engineers’ bread and butter.
Titanium
The element titanium (Ti) was discovered in 1791, but the metal wasn’t typically used in aviation/aerospace until around the start of the Cold War. The X-3 research aircraft (1952) was the first to have some of its major components made of titanium. The F-100 Super Sabre (1953) also utilized titanium extensively, and the famous SR-71 Blackbird family of reconnaissance jets of the early-to-mid 1960s were the first to employ Ti in the bulk of their construction, comprising around 85% of the aircraft. The 1959 Mercury spacecraft capsule’s pressure vessel was made of a nickel alloy, but had an outer shell of titanium to help protect from the heat of reentry (along with its ablative heat shield on its bottom surface).
Over the past few decades, titanium alloy has transitioned from the exotic, “unobtanium” category, where nobody could afford to use it other than advanced militaries or the Skunk Works, to one of the most widely used superalloys in aviation and aerospace.
Titanium is extremely strong for its weight, has excellent heat-shedding properties, and self-oxidizes into a stable, durable surface. For this reason, the modern aerospace industry is the number one customer for titanium alloys. According to TMS Titanium, countries that have considerably large military budgets, like the United States, drive the high demand for titanium and even consider the availability of the metal a matter of national security.
Due to titanium’s excellent performance, growing availability, and reasonable price, today’s commercial aircraft such as the Airbus A380 and Boeing 787 utilize much more titanium than previous aircraft designs. Despite the growing use of Ti in commercial aviation, the largest consumer remains the military/aerospace industry. Many military aircraft such as the F-22 Raptor, F/A-18, C-17, F-35 and Black Hawk helicopter require large quantities of titanium to produce, and the tank-killing A-10 “Warthog” features a thick “bathtub” of titanium armor surrounding the pilot.
Titanium’s lightness is one of its primary benefits, and a lighter aircraft or rocket means less fuel is required, and more payload is available. Titanium alloys have been replacing aluminum due to their superior strength, as well as Ti superalloys’ superior ability to resist heat and corrosion when coming in contact with carbon-fiber reinforced polymers (CFRPs) – more on those below. Titanium is commonly used in all types of fasteners, airframe components, and landing gear, as well as engine components such as fan blades, discs, shafts, and casings.
Titanium powder metallurgy is another aspect of the metal that has grown in aerospace and military use, where, instead of requiring difficult and time-consuming machining processes, parts and components can be manufactured from titanium powder that is consolidated or finalized via metal injection molding, sintering, hot isostatic pressing, direct powder rolling, or laser engineered net shaping methods, including “printing” or additive manufacturing.
Niobium superalloys
Rocket scientists are pretty smart folks, and though they often use well-proven materials such as Inconel, they never stop striving for improvements and innovations. One important breakthrough that happened quite recently (near the end of 2021) was the patenting of a new niobium superalloy by the Air Force Research Laboratory in Dayton, Ohio.
The US Patent (number 11,198,927) is titled “Niobium alloys for high temperature, structural applications.”
Niobium (Nb) – formerly known as columbium in America – isn’t new, being discovered in 1801 and distinguished from the closely related tantalum in 1864. Historically niobium has been used as an alloy hardener component in producing pipeline steel, but, like many other superalloys, became the focus of intense research during the 1950s and 1960s “Space Race” because of its ability to handle extremely high temperatures, making it useful for rocket engine nozzles and jet engine exhaust components.
For aerospace applications today, the most useful forms of niobium are the alloys known as C-103 and C-3009, which can be welded or otherwise fashioned into structural elements such as rocket thrust cones and high-temperature valves.
The problem until now has been, as pointed out by TechLink’s Troy Carter, that these alloys “contain rare and expensive metals such as hafnium ($1,420/kg), tantalum ($850/kg), and zirconium ($360/kg). They also oxidize above 600° Celsius and so require coatings.”
However, Carter continues, “Air Force researchers, Kevin Chaput (now at Northrop Grumman), Oleg Senkov of UES, and Todd Butler of AFRL’s Materials and Manufacturing Directorate, created their own niobium alloy that’s 30% molybdenum, which is highly resistant to corrosion and has one of the highest melting points of all metals – it’s also way cheaper at $100 per kilogram. Add a touch of titanium, a sprinkle of iron, and just a pinch of zirconium, and Voila! You’ve got a high-performance, lower-cost alternative for structural applications with improved oxidation resistance. They named it M3F, and conducted lab tests to characterize it.”
High corrosion resistance, one of the highest melting points, good strength, and “way cheaper”? Sounds like a winner to us.
Cobalt-based superalloys
Cobalt (Co) has been a component of many superalloys, including several Inconel or nickel-based alloys, for many decades. However, recent discoveries have led researchers to understand some unique benefits of fully cobalt-based, rather than nickel-based, superalloys. Authors Brandon Ohl et al. of Dunand Research Group/Northwestern point out that cobalt alloys can be processed so as to have similar cuboidal microstructure as Ni-based superalloys, but without some of the latter’s downsides.
This is potentially quite significant, as the cobalt-based superalloys demonstrate solidus (melting point) temperatures that are 100°-150°C (roughly 212°-300°F) higher than optimized nickel-based superalloys, which allows for higher operating temperatures for increased performance and/or reduced environmental impact and efficiency due to a cleaner burn. The authors continue, “In addition to higher temperature capabilities, the Co-based superalloys improve upon Ni in several other ways. Preliminary studies have shown that it is likely that Co superalloys can be processed into large single crystals (a form needed to achieve good high temperature creep resistance) without forming solidification defects on their surface (so-called freckles) that plague Ni-based superalloys.” Pretty nifty!
Advanced composites for use in aerospace
We’ve seen that there’s a temperature ceiling, or a limit, which all-metal alloys currently can’t exceed (even though the latest cobalt-based alloys are stretching those limits somewhat). In addition, design/manufacturing limitations due to material properties and structural considerations are spurring the need for advanced composites for aviation and space applications. Researchers have developed or are developing such materials as fiber-reinforced polymer composites, ceramic fiber composites, self-healing composites, self-sensing composites, 3D fabric structures, directionally oriented fabric structures, fiber-metal laminates, glass fiber composites, laminated composites, metal-based laminates, sandwiched composites, braided composites, and even polymer nanocomposites.
In very simple terms, AviationPros.com points out, there are essentially two main types of composites where aerospace is concerned, and most of the subcategories are variations of these two: Fibrous composites, and particulate composites. The most well-known types of fibrous composites are likely glass-fiber reinforced plastic or “fiberglass,” and carbon-fiber reinforced plastics, often shortened to “carbon fiber.” In these composites, glass or carbon fibers, which are strong and stiff (relative to their density) but hard and brittle, are combined in a polymer matrix or resin, which is tough but not particularly stiff or strong. By combining the two materials, a composite that possesses most or all of the benefits (high strength, stiffness, toughness, and low density) of each is created, with little to none of the weaknesses of the individual component materials.
Less well-known composites are particulate composites, in which (usually) non-metallic particles are suspended in a metallic matrix, such as silicon carbide particles combined with an aluminum alloy.
The benefits of fibrous composites have become well-known, due to their exceptional strength-to-weight ratio when combined and overlapped in layers that help overcome the material’s anisotropy, or its natural tendency to fail directionally according to the orientation of the fabric or fibers in the composite matrix. Unlike superalloys, fibrous composites can also be formed into nearly any shape with relative ease, without the material limitations to milling or finishing associated with many tough metals. Polymer composites are typically resistant or immune to corrosion, unlike metals. Additionally, pre-formed composite shapes can be easily assembled into larger sections, without the need for drilling lots of holes and riveting smaller metal sheets or component pieces to create a larger unit. This can greatly reduce assembly time and prevent fatigue or failure where holes are drilled and natural stress risers occur.
Composites have some disadvantages as well, namely a typical increase in the time needed for forming of the composite parts themselves, which is usually a labor-intensive process with many layering/curing/inspecting cycles throughout. Cost can become a factor as a result. Also, since larger, seamless composite shapes are commonly used, if one part of a composite structure fails in a key structural area, potentially the entire piece would need to be replaced, rather than being able to remove one superalloy section and replacing just that failed component piece.
Among the first uses of composites in aerospace was in the stabilizing tail surfaces of the F-14 and F-15 fighter aircraft. Initially, composites were used only in secondary structures, but as knowledge and materials have improved, advanced composites have become more common in larger, primary structures like airframes, wings, and fuselages of aircraft and spacecraft.
AviationPros explains, “Initially, the percentage by structural weight of composites used in manufacturing was very small, at around 2 percent in the F15, for example. However, the percentage has grown considerably, through 19 percent in the F18 up to 24 percent in the F22. The AV-8B Harrier GR7 has composite wing sections and the GR7A features a composite rear fuselage. Composite materials are used extensively in the Eurofighter: the wing skins, forward fuselage, flaperons and rudder all make use of composites. Toughened epoxy skins constitute about 75 percent of the exterior area. In total, about 40 percent of the structural weight of the Eurofighter is carbon-fibre-reinforced composite material. Other European fighters typically feature between about 20 and 25 percent composites by weight: 26 percent for Dassault's Rafael and 20 to 25 percent for the Saab Gripen and the EADS Mako.”
Commercial aircraft companies, ever in pursuit of lighter weight and more fuel-efficient designs, have adopted the new composites with enthusiasm. For example, the Boeing 787 aircraft is comprised of an incredible 80% composite (mostly carbon-fiber) by volume. By weight, its material contents are 50% composite, 20% aluminum, 15% titanium, 10% steel, and 5% other. The 777, 767, and Airbus A320, A340, A380, A350-1000, and A300-600 all make use of a significant amount of composites.
Ceramic matrix fiber composites
One exciting aspect of advanced aerospace composites, in addition to their low weight, easy component assembly, and high strength, is their potential for even greater heat resistance than the superalloys. Some experts suggest that “The development of nickel and cobalt-based superalloys are at their limits of use in terms of new environmental requirements, i.e., to obtain high efficiency (fuel economy, lower operating costs) and a reduction in pollution (noise level, emissions). One solution would consist of increasing the temperature of gases in the hot parts of the aircraft engines. The alloys currently used are limited to temperatures close to 1100°C and monolithic ceramics exhibit behavior too brittle for application. Only ceramic matrix composites (CMCs) are potentially able to fill the necessary requirements. Thus, [superalloys’] gradual replacement by composites… [has] accelerated over the past twenty years.”
Todays’ structural ceramic matrix composites generally consist of a fibrous reinforcement which constitutes the “skeleton” of the whole, and of a matrix which embeds the fibers. Both of these components may be made of different materials, with different performance goals and attributes. The different CMCs are commonly designated with the first material designating the foundational fiber, and the second denoting the material of the matrix, as in carbon/carbon, carbon/silicon-carbide, oxide/oxide, etc. You may have heard “carbon/carbon” in reference to the nose cone and leading wing edges of the Space Shuttle, for example.
Current CMCs have much lower densities than even superalloy-based metallic materials and can potentially survive in higher temperature environments and applications. Efficiency goals are requiring components to survive in high-stress, super-high-temperature (1400°C/2550°F) environments were strength, oxidation, and corrosion are key considerations, while at the same time guaranteeing performance at least equal to those of superalloys in terms of thermal conductivity, mechanical resistance, and service life. Multiple research programs have been set up for the development and study of advanced CMCs for these reasons.
Braided composites
Braided composites, particularly the latest three-dimensional full five-directional (3DF5D) variety, demonstrate superior fatigue strength, improved impact resistance (to bird strikes, for example), and reduced weight compared to many “standard” fiber composites, and are beginning to be used in aviation/aerospace (the Airbus A350-1000 was one of the first to utilize braided composites in a significant way, and its wingskins are the largest-ever civil aircraft composite parts).
Braided composites are exactly what they sound like, wherein the (typically carbon) fibers are interwoven or braided together in specific ways before being set in the resin, polymer, or ceramic matrix. The braided composite’s complex interlacing geometric structure improves its strength and performance, and helps reduce the perpetuation of cracks along fibers, which can be a problem for non-braided fibrous composites.
Additionally, radial braiding can help improve tubular strength along the x and y axes of spacecraft. Due to their demonstrably superior performance, it is likely that we will soon be seeing more widespread use of braided composites beyond aerospace applications.
Polymer nanocomposites
Polymer nanocomposites currently represent the bleeding edge of high-performance aerospace materials. As we discussed above, fibrous, or fiber-reinforced composites have a well-deserved reputation as excellent materials for aerospace applications, exhibiting higher strength-to-weight ratios compared to many metals. However, over the last two decades, many researchers’ focus has been shifted towards nanomaterial-based composites, which have shown potential improvements in material properties and multifunctional performance compared with even the most advanced fibrous composites.
As Muhammad Adeel Ahsan of AZoNano explains, “Nanocomposites are heterogeneous materials engineered by combining polymers and inorganic solids with incredibly small dimensions that take advantage of unique physical and chemical features found at the nanoscale.” The nanoparticles used may be of spherical, cubic, platelet, flake or other shape, and may be of regular or irregular geometry.
For aerospace, lightness, strength, and resistance to UV rays and heat are always top priorities, and the new polymer nanocomposites offer unique benefits compared to other materials. Ahsan points out that these nanocomposites can survive in diverse environments, including changes in temperature, moisture, and dynamic pressure, and even lightning strikes, due to their excellent electrical, chemical, thermal, and mechanical properties. In addition, today’s advanced polymer nanocomposites have exceptional resistance to corrosion, impacts, and fatigue, and exhibit superior strength, toughness, and scratch resistance, due to the nanofillers used, which basically have a defect-free crystal level structure.
Aerospace continues to push the envelope of “next-gen” materials with improved performance, lighter weight, and greater versatility. We’re excited to see how today’s “cutting edge” aerospace manufacturing materials and processes perpetuate into more aspects of society. It’s fun to think about what might be the “next-gen” in 20 or 30 years.
–By Jeff Davis, Intergalactic Scribe
Sources:
https://nickelinstitute.org/en/blog/2020/may/back-in-the-game/
https://www.corrotherm.co.uk/blog/inconel-alloy-625-in-aerospace-engineering
https://www.ulbrich.com/blog/inconel-718-vs-inconel-625-battle-of-the-titans/
https://en.wikipedia.org/wiki/Inconel
https://tmstitanium.com/news-post/titanium-and-the-aerospace-industry