We shaked, baked, and beat up a bunch of thermal management components and got them qualified at TRL 8
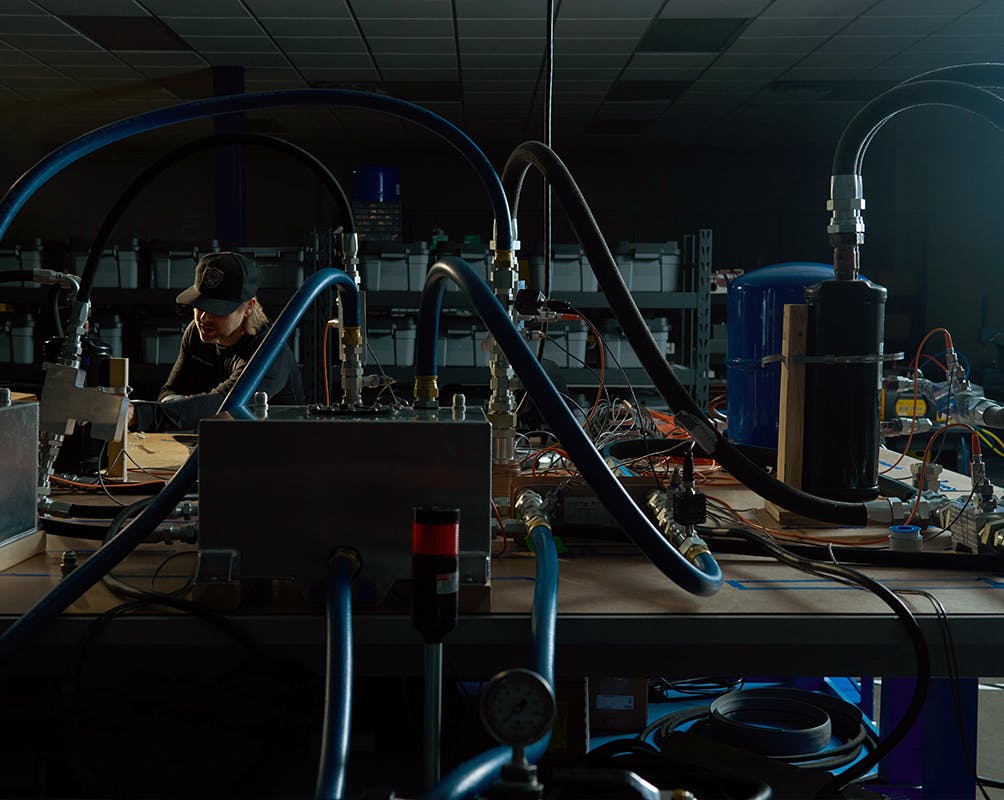
Blog
They say if you love something, set it on fire, smash it with a sledgehammer, and zap it with lightning. Wait, no, they don’t say that, and you shouldn’t do any of those things to the beloved people, pets, or houseplants in your life. However, if the thing you love is an advanced thermal management system that needs to perform in the most extreme airborne conditions, you need to put it through hell at some point.
That’s precisely what we did, and we’d like to tell you all about it in this post.
First, you should know that we routinely do testing on our thermal management systems and components (remember when we blogged about the 100-hour test results?), either for ongoing internal research, development, and validation or as part of military, commercial aviation, or space program requirements. We don’t blog about all of it, but this battery of tests is significant because (1) the tests were extremely rigorous, and (2) the result is a bunch of our hardware is now qualified at TRL 8 (more on this below).
Let's dive in.
What’s the TL;DR?
Oh, you don’t want to read the whole blog post? Candy Crush calling your name? Gotta get in that Duolingo lesson for the day? OK, fine. Here’s a summary from our senior thermal engineers.
We put a thermal management system comprising several key components through a battery of tests which simulate an environment more severe than what is encountered on a military supersonic fighter jet. An exaggeratedly severe environment is used to ensure the system/component has margin to perform and survive above and beyond real-world conditions. Further, this testing aims to compress an entire 20-year service life into an accelerated test to ensure long-term survival and operation. Successful completion of qualification testing validates system performance against system performance and environmental requirements, ensuring the system will provide reliable performance with margin across all operational conditions.
Which components were tested?
Hey, you still here? Did you pause notifications or just decide not to be a slave to thirsty smartphone apps? In any event, we’re glad you’re still reading!
Every thermal management system is really an integration of subsystems and component parts. If any of them fail, the whole system is at risk, so we’re happy to report that the following branded Intergalactic equipment items passed these hellish tests with flying colors:
- Boreas3 Heat Exchanger
- HydraX Pump
- Carina1 Power Distribution Unit
- Fornax Electric Heaters
- Aries1 Controller
- Libra4 Scroll Compressor
- OrionXD Accumulator
All of these components have undergone rigorous testing in the past, including our famous, patent-pending microtube heat exchanger, the Boreas3, surviving 14,000 PSI without a leak in an ultra deep-sea dive.
What tests did we run?
Hey, are you multitasking? Are you watching the last episode of Better Call Saul while reading this? Listen, no spoilers, but it’s not the redemptive ending you got with Breaking Bad. That’s all we’ll say. It’s good, just not what you might expect.
Ok, you’re still here, eagerly awaiting the skinny on which punishing paces we put our stuff through. Your wait is over, friend:
- Endurance vibration exceeding Mil-Std-810G 514.6 Procedure I, with 10 hours per axis, representing two lifetimes of service duty. Basically, we shook the crap out of everything for a long time to ensure operation under beyond worst-case conditions and ensure a lifetime without mechanical failure.
- Functional shock exceeding Mil-Std-810G 516.6 Procedure I, with peak force of 27 Gs. Can you imagine a large, muscular, and ill-tempered man smashing a thermal management system with a sledgehammer? That is pretty much what this test simulates.
- Standard shock per Mil-Std-810G 516.8 Procedure II. OK, we admit this one isn’t as dramatic. It’s basically subjecting the thermal unit to a bunch of small impacts to simulate transportation and handling by some of the world’s least careful shipping clerks.
- Flight and non-flight temperature per Mil-Std-810G 501.5 and 502.5, with operational temperature from –40 to +71 Celsius and non-operational temperatures from –54 to +71 Celsius. We blasted the unit with extreme temperatures to simulate the far edges of what might be possible in the air and on the ground.
- Temperature shock per Mil-Std-810G 503.5 Procedure I-C, with temperature ranging from –40 to +71 Celsius, with a 50-degree C change per minute. Same as above, but we ramped up the thermal stress with rapid temp changes over a bunch of cycles. Imagine bouncing between the sauna and the ice tub, except it’s much hotter and colder and you’re a piece of robust hardware and not a carbon-based lifeform with an organic heart that needs to keep beating.
- Humidity per Mil-Std-810G 507.6 Procedure II. We ran the unit in an environment more humid than the worst summer day in south Florida. We’re talking those Florida days where it’s taco pits as far as the eye can see and even the swimming pool doesn’t cool you down.
- Altitude and pressure cycling per Mil-Std-810G 500.5 Procedure II, sea level to 65,000 feet above sea level. Imagine being sling-shotted from ground level to a spot more than 12 miles into the sky, a rarified air only reached by the most advanced military fighter jets. That’s this test.
- Rapid decompression per Mil-Std-810G 500.5 Procedure III. This is kind of like the altitude test but instead of focusing on extremes, it’s meant to simulate rapid changes in altitude, like steep climbs and dives. Like, say Maverick is on a mission and sees a random tower and his impulse to buzz it kicks in, but it’s 10k feet below. You’d want to know the thermal systems could handle that maneuver, Mav.
- Explosive environment per Mil-Std-810G 511.5 Procedure I. Haha, blowing stuff up! Yes! Heck yes! Well, it’s actually the opposite of that because if things had blown up, we would have failed this test. We placed the unit in a chamber filled with hot jet fuel vapor and flipped the power on to ensure it won’t cause a fire or explosion.
- Indirect lightning effect per RTCA DO-160G 22.5.1.2. The “indirect” part of this test name might be a little misleading because we literally zapped the input power leads to ensure the system and components would survive if struck by lightning while in flight.
- Input power testing per Mil-Std-704E. For this one we just ran the unit with a wide range of power conditions to mimic changes in aircraft power and ensure smooth operation.
- Electrostatic discharge protection per Mil-Std-461G CS118 and IEC 61000. More shocks! Haha, yes! Heck yes! We applied small shocks to all electrical pins to make sure any ESD during handling and installation wouldn’t damage the hardware.
- Our sadists, er, engineers weren’t done yet! We also did cyclic thermal environment testing on the Aries1 Controller, Carina1 PDU, and motor controllers for the HydraX Pump and Libra4 Scroll Compressor. We ran 500 cycles with temperature ranging from –40 to +71 Celsius at 17 degrees Celsius per minute to mechanically stress the system electronics and ensure lifelong survival.
Phew! That’s a lot of abuse for hardware and software systems that did nothing to deserve it. But, they came out the other end with flashy new credentials: qualified TRL 8.
What does TRL 8 mean?
Glad you asked! Technology Readiness Level, or TRL, is a measurement system that the defense aerospace, civil aviation, and space sectors use to determine the maturity level of various technologies. The scale basically tells you how “flight-ready” a technology or product is because you don’t want to use unproven stuff in air or space.
The TRL scale goes from 1-9, with 9 being the highest maturity level. So, TRL 8 is super good, but of course we never rest until every thermal system or component we develop is rated TRL 9. More to come, so stay tuned.
Update: We've upgraded to TRL 9 (August 2023)
So, remember how we told you we'd keep you posted? Well, this is us making good on that promise.
Achievement unlocked: TRL 9. Yes, all the components listed in this post went through a series of flight tests in recent months and passed with flying colors. That means these components are now "system proven" or "ready for full commercial deployment." That's what TRL 9 means, bro! Our stuff is ready for whatever mission you want to throw at it.
- Brad Plothow, Social Media Intern