A brief overview of air-cycle thermal management systems
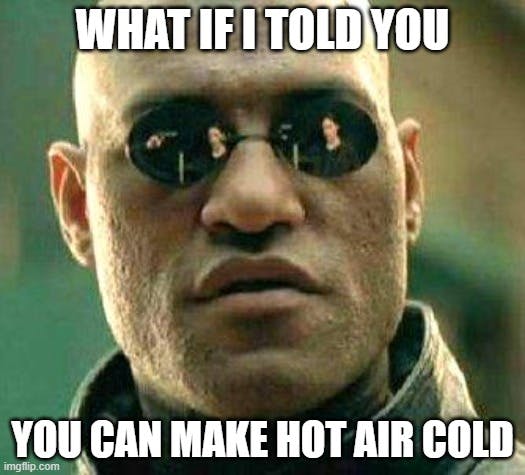
Blog
If you read that title and suddenly felt drowsy, hold on there, bub! Air-cycle systems are actually pretty, uh… cool. (See what we did there?) Air-cycle cooling systems are widely used on jet airliners due to their ability to make cold air out of hot air using just… air! It sounds like magic, but it’s really just clever use of engineering and a keen understanding of the laws of thermodynamics. Let’s go over the basics of these effective, environmentally friendly cooling systems that make modern air transport possible (and comfortable).
Air-cycle cooling systems have roots in the 19th century
The basic premise behind air-cycle cooling is that when air is compressed, it heats up, and when it’s decompressed, it cools down. You may have noticed this when using an “air duster” or can of compressed air, which can get painfully cold when discharging. Several inventors developed cooling systems based on compressing and decompressing air in the last half of the 19th century. A notable pioneer was Joseph James Coleman, a Scottish inventor who was approached by naval shipping brothers Joseph and Henry Bell and asked to develop a method for keeping beef cold long enough for international transport aboard ship. The Bell-Coleman refrigeration compressor was the result.
In very simple terms, Coleman’s machine consisted of a compressor and turbine on a common shaft, with dual heat exchangers, one associated with a heat reservoir and one associated with a cold reservoir or refrigerator. The air flows from the hot/compressed portion of the compressor, through the first heat exchanger which sheds some of the heat, then back into the turbine portion where it loses pressure and thus drops in temperature, then out of the turbine and through a heat exchanger that cools whatever you want to be cold. This heat exchanger can be connected to a solid heat sink, or piped water, or pretty much anything that can retain cold temperatures.
Refrigeration ships, or “reefers,” became very popular and allowed long-distance shipping of frozen and refrigerated goods for the first time in history. The design was so influential that the Bell-Coleman Cycle became a common term in refrigeration and fluid dynamics, defined as a refrigeration cycle where the working fluid (most often air) is a gas that is compressed and expanded, but does not change phase. This is also known as a “reverse” Brayton cycle.
Modern air-cycle thermal management systems follow the same principles
Today, the most common use of air-cycle systems is in jet airliners and other large jet aircraft, where they are employed to maintain crew and passenger comfort, assist in maintaining cabin pressure (where appropriate), and cool the avionics. The air cycle machine (ACM) is the cooling/refrigeration unit that is part of the environmental control systems (ECS). Today’s large passenger airliners typically have two or three ACMs, which are also known as “air conditioning packs” or simply “packs.”
Unlike vapor-cycle air-conditioning systems (commonly used in homes, buildings, and automobiles), which use phase-changing liquids/gases such as Freon, the air-cycle system uses, you guessed it, air. This has several key advantages for this application, which we’ll discuss later.
How does an air-cycle machine (ACM) work?
In simple terms, when the jet engines are running, “bleed air” is taken from the compressor stage (technically known as the high-pressure compressor or HPC) and is regulated by a control valve. It’s called bleed air because it’s “bled off” the engine. Since it’s high-pressure air scavenged from the super-hot compressor stage, the bleed air is too hot to be efficiently used directly by the air-cycle machine, so it is first sent through a primary heat exchanger where it is cooled by cold air taken from the intake stage of the engine. Pre-cooling the bleed air via the primary heat exchanger increases the efficiency of the ACM by lowering the temperature of the air entering the ACM’s compressor. (Since the energy required to compress a gas by a given ratio rises as the temperature of the incoming gas rises, using cooler air means that less work is required to compress the air.) The air is then piped into the ACM, which, like the 19th-century Bell-Coleman machine, consists of a compressor and a turbine connected to a single shaft (similar to a very basic jet turbine engine, but obviously without the fuel ignition, thrust chambers, or turbofans).
In the compressor stage of the ACM, the air increases in pressure, and also of course in temperature. So, that air is then routed through another air-to-air heat exchanger, typically known as the secondary heat exchanger or sometimes the “main” exchanger. The cold air for this heat exchanger is known as “ram air” and is provided by the ram-air intakes in the fuselage or wings of the aircraft when in motion. (After cooling the compressed air from the ACM, this ram air is vented overboard.)
The now-cooled air from the ACM compressor stage is routed back into the turbine section of the ACM, where it drops dramatically in pressure and thus in temperature. This cooled, conditioned air is passed through a water separator to remove excess water vapor, and is then combined with filtered, recirculated air from the aircraft in a device called a mixer unit. From the mixer unit, the fully conditioned and dehumidified air is then routed through the cabin and cockpit via axial fans to maintain a comfortable temperature for crew and passengers. Automatic environmental control systems work throughout the flight to regulate the mixture of the hot bleed air from the engines (which is also often used in deicing wings and control surfaces) and the cold air from the ACMs.
The ACMs and the ECS are also integral to keeping the aircraft cabin pressurized at high altitudes, which is what enables passengers and crew to, you know… breathe. To keep the aircraft cabin pressure at a safe level, the incoming air is held at a set pressure within the cabin using an automatic outflow valve. This valve opens and closes on a regular basis to release the incoming air at the rate regulated by pressure sensors. The outflow valve also allows old, stale air to exit the plane.
In ships, trains, or land vehicles, the compressor for an ACM is usually driven by electricity, steam, or in some cases turbochargers (the first primitive air-compressor-based refrigeration or ice-making machines could even be driven by horses, mules, or a windmill). However, the compressed air necessary to drive the air-cycle machine aboard an aircraft is taken either from the Auxiliary Power Unit (APU) or from the engines, when they are running. (The APU is essentially a jet turbine that is set up to provide electrical power to run the aircraft’s onboard systems, rather than providing thrust, and is typically only run when the aircraft is on the ground.)
Why use hot bleed air to generate aircraft cooling?
If, like us, you geek out about all things aviation, aerospace, and ECS, you may wonder why engineers go through the trouble of using hot bleed air from the compressor stage of a jet engine to make cool air for the aircraft. After all, isn’t there enough cool air outside at 550 mph and -40° air temperature at 35,000 feet?
Your intrepid author asked a lot of stupid questions to a lot of smart people at Intergalactic as well as aircraft technicians in both civilian and military aviation circles, and here’s the down-low from several techs and pilots.
“Using bleed air allows the pressure to be regulated. Using it straight from the intake flow does not allow that, as it is limited to the ambient pressure or ram air pressure (airspeed during flight).”
Another smart person adds, “It’s a mass flow issue. The cool air at the intake doesn’t have enough pounds per minute at ambient to send to the system to work properly. It could be done but the size of the system would be weight- and space-prohibitive. It’s easier to tap high-pressure, high-flow air from the HPC and add an exchanger to handle the adiabatic efficiency issue.”
Additionally, the air needs to be compressed in order for the ACM’s compressor and turbine to function. “The ACM has its own turbine/compressor that needs the high pressure engine air to power that turbine. In addition, the pressure drop downstream of the ACM turbine is what releases lots of heat and provides the desired cooling effect.”
Interestingly, in today’s aircraft equipped with high-bypass-ratio turbofan engines, the bleed air is tapped off the lower compressor stage most of the time, with the high pressure port providing air only when there is an increase in bleed air demand. As a result, even the compressed bleed air provided by the jet turbine must be further pressurized before it can provide enough energy to be of effective use in maintaining comfortable cabin temperatures and pressures for a large aircraft. That's where the ACMs come in to finish the job.
Why not just use ram air from the ram-air inlets during flight?
We asked one tech why the air for the ACM couldn’t be provided by ram-air intakes when the aircraft is at speed. The response: “The very high pressure drop at the turbine stage of the ACM is what reduces the temperature of the air, which is then safe enough to be passed into the cabin. Therefore, the higher the pressure of the air the turbine receives, the greater will be the temperature drop. If ram air were used, you would still need a larger [and heavier, and bulkier–Ed.] compressor and a turbine to increase the pressure to the desired level.”
Primary advantages of an air-cycle cooling system
So, what are the main reasons for using an air-cycle cooling system on large aircraft? Let’s go over the “pros” of this type of ECS.
- No coolant chemicals or leaks. The working fluid of this system (air) is free, safe, and non-toxic. In a world increasingly concerned about CFCs, ozone damage, global warming, and other environmental concerns, a cooling system that runs on air is a distinct advantage.
- Reliability is high, maintenance is low. Modern ACMs are very reliable, resulting in a reduction in maintenance costs and downtime.
- Improved performance when outside its ideal operating range. Compared to typical vapor-cycle systems, air-cycle systems exhibit relatively better performance when operated in circumstances outside their design range.
- Greater temperature difference between hot and cold components. Compared to common vapor-cycle systems the difference between the “hot side” and “cold side” in an air-cycle system can be much greater. This means you can produce near-cryogenic temps on the output/cold side while also generating useful heat for other purposes (such as cabin heat or deicing).
Some downsides include size and weight, and the need for high-pressure bleed air to run the system. Without a powerful jet turbine or APU running, an air-cycle system doesn’t make a lot of sense from a size-versus-performance perspective. This is why nearly all compact heat exchanger systems for military, eVTOL, or aerospace applications use vapor or liquid-cycle systems that are more efficient relative to their size and weight.
Today, air-cycle cooling systems are used primarily on large airliners and similar cargo/transport aircraft, though there is some use on trains such as the German high-speed ICE (InterCity Express). There is some interest in incorporating the use of turbo-enabled air-cycle systems for cooling and refrigeration of smaller transport vehicles. In theory this would help alleviate the problem of chemical refrigerants, which are typically environmentally hazardous and/or corrosive.
So now you know how you can sit comfortably in a pleasantly cool, pressurized vessel flying at 35,000 feet, traveling at over 550 miles per hour, sipping a chilled Diet Dr. Pepper and munching on a Biscoff. Ain’t modern technology wonderful?
–By Jeff Davis, Intergalactic Scribe
Sources:
https://www.grimsby.ac.uk/documents/frperc/research/aircycle_research.pdf
https://en.wikipedia.org/wiki/Air_cycle_machine
https://docs.lib.purdue.edu/cgi/viewcontent.cgi?article=1347&context=iracc
https://resources.wolframcloud.com/FormulaRepository/resources/Bell-Coleman-Cycle#
https://www.tronair.com/resources/aircraft-cabin-pressurization-guide/