2024-11-04
On Reaction Engines and the future of microtube heat exchangers
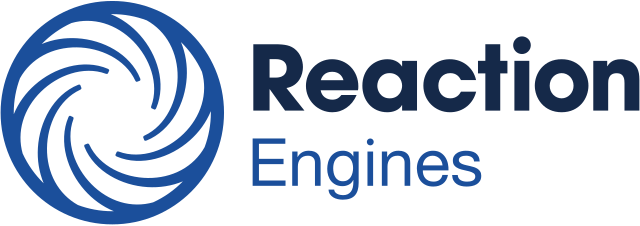
Blog
We were extremely saddened by the recent news that Reaction Engines is entering “administration” in the UK and winding down its operations in Great Britain and Colorado. Reaction Engines was founded 35 years ago with a pioneering concept in single-stage-to-orbit hypersonic propulsion and expanded its business model by selling thermal management products – notably microtube heat exchangers – into various industries.
Yes, Reaction Engines was a direct competitor with Intergalactic in the aerospace thermal management market, and yes, they were one of only a few players (including Intergalactic) offering microtube heat exchangers. Yet, our teams had become quite close over the years, and we were rooting for their success, not only due to the promise of their hypersonic engine technology but also because we believe microtube heat exchangers are poised to replace plate fin as the industry standard in air and space.
We aren’t privy to all the details of Reaction Engines’ shuttering, but it seems clear that the famous aerospace “valley of death” is a factor. Far too many promising companies struggle to make the transition from development to production, in part because the aerospace industry is set up to favor entrenched incumbents. The modern aerospace sector was forged on the anvil of unprecedented innovation in the mid 20th century but has been dominated by incentives and a mentality which is heavily resistant to taking on any risk, regardless of potential, due to an outsized focus on short-term financial rewards. That makes it harder for companies with promising technologies to make the leap from prototyping to mass manufacturing.
In the wake of the Reaction Engines news, some may question the viability of microtube heat exchangers – one of RE’s core products – and its future in aviation, defense, space, and beyond. It would be a mistake to conflate the complex challenges of building and growing a multinational company with the viability and superiority of microtube technology. Let’s unpack the reasons why microtubes are here to stay.
About microtube heat exchangers
First, some quick background. Heat exchangers transfer heat from one fluid media to another and are the heart and soul of most thermal management system designs for aircraft and spacecraft. In aerospace, the dominant heat exchanger technology, plate fin, was invented over a century ago, in 1923. With 100 years of development and incremental improvements over time, plate fin is a well proven technology with lots of qualified off-the-shelf designs. It’s also fundamentally limited and facing obsolescence across a growing number of crucial technical categories.
Microtube heat exchangers have been a concept in thermal engineering texts for a long time, but their commercialization is a recent phenomenon. Microtube heat exchangers take advantage of physics to dramatically reduce size and weight, which is increasingly critical for modern aerospace applications. You can go deeper on the physics, engineering, and benefits of microtube heat exchangers here.
Microtube heat exchangers are important because they are part of a holistic technology upgrade to the thermal management technology stack. We need innovative thermal tech to enable vital new capabilities on military and civilian aircraft and help the U.S. win the second space race. Thermal management is a constraining problem for aerospace innovation – if you can’t regulate temperature, nothing else matters. So, modernizing the thermal tech stack is an urgent need, and microtube heat exchangers are an important place to start. We’ll explain why.
Systems first, platforms second
In the military aerospace sector, the Air Force has been moving to a “systems first, platforms second” approach to developing and procuring technologies for use on military aircraft. This shift is necessary because the rate of technological advancement is moving faster than the military’s ability to develop, test, qualify, and field new platforms. The only way forward is to develop flexible, scalable systems that can be rapidly modified and deployed across a wide range of platforms.
So, what “systems” need to be developed? The heart, lungs, and circulatory systems of modern military aircraft are propulsion, power, and thermal management systems. In the past, these domains were developed and procured in silos. Moving forward, they require tight integration. This means thermal management systems need to account for increasing power requirements and smaller footprints for the thermal system – competing pressures that mean compact, lightweight, and native high voltage capabilities are becoming table stakes.
Similar trends are happening in civil aviation, where trillion-dollar markets are emerging around electrification and the development of electric and hybrid-electric urban air mobility and regional air mobility platforms. These new aircraft require the same characteristics noted above – small, lightweight thermal system with native high voltage capability.
Size (and weight) matters
These trends are putting major pressure on thermal systems suppliers to innovate, which is especially challenging for companies that have enjoyed decades of success from selling incremental modifications of legacy technologies. The economic incentives and innovation pressures in the aerospace industry are not always well aligned, and this is especially true for thermal management, which was historically viewed as a commodity but increasingly is becoming enabling for upstream innovations.
This is where microtube heat exchangers re-enter the chat. How do you get size and weight out of thermal system designs while maintaining or increasing capacity, performance, and robustness? You can’t keep playing incremental games with old technologies. You must prove out new technologies in the development and production environments. Of all the core technologies that go into thermal systems, microtube heat exchanges are perhaps the most promising and furthest along in delivering on that promise.
There is no near-term path to achieve the kind of size and weight savings that are necessary without microtube heat exchangers. It’s that simple.
Reasons to believe
Reaction Engines was an engine-maker that pursued microtube heat exchanger technology to enable their novel hypersonic concept. At Intergalactic, we’re thermal systems developers which pursued microtube heat exchangers to hit extremely aggressive size and weight targets with our customers. In both cases, our companies have made major inroads in developing this new technology platform with the shared belief that microtubes would replace plate fin as the industry standard soon.
At Intergalactic, we believe for a variety of reasons:
- Something has to replace plate fin. It’s been a reliable and useful technology, but its limitations are becoming a point of urgency across the military and commercial aerospace sectors. Microtube technology is the next evolutionary step.
- In our fairly extensive experience, microtube heat exchanges consistently cut one half to two thirds of the weight compared to a comparable plate fin heat exchanger, offering the kind of mass savings that make a big difference across a wide range of aerospace applications, including bleed air precoolers, ram air heat exchangers, vapor cycle system evaporators and condensers, and much more.
- Between Intergalactic and Reaction Engines, the microtube technology platform is extremely well tested. For our part, we’ve put stainless steel and Inconel microtube heat exchangers through 27 G’s of force, 14,000 PSI of pressure, and full Mil-810 and DO-160 environmental qualification on military fixed and rotor-wing aircraft, with full commercial qualification coming soon.
On that last point, Intergalactic is (we think) the only company in the world to fully flight qualify and flight test a microtube heat exchanger. We’ve had it flying as part of a vapor cycle system we designed for a fifth-generation military fixed wing fighter since the middle of 2023. We had heard rumblings that Reaction Engines was going to have an opportunity to flight qualify and test a microtube heat exchanger on a commercial platform soon, and we were rooting for their success to advance the technology.
What’s next for microtube heat exchangers?
At Intergalactic, we’ve taken microtube technology to TRL 9 and we’ve been busy building the capabilities and processes to ramp up manufacturing for full scale production across a wide range of applications. Our confidence in this technology starts with our patented and proprietary laser welding manufacturing process, which has provided the robustness required to perform under the most rigorous conditions. We’ve also been expanding into new materials – ranging from stainless steel to Inconel to titanium – and developing curved applications to conform to engine nacelles and aircraft fuselages.
With the wind-down of Reaction Engines, some in the industry may wonder if the future of microtube heat exchangers is in doubt. The evidence strongly points in the other direction. If anything, the fact that Reaction Engines’ microtube heat exchangers found a market before their truly novel hypersonic engine is a testament to how critical microtube technology is for both military and civil aviation right now.
At Intergalactic, we’re heartbroken that our friends at Reaction Engines met the end of their road, and we’re even more motivated to take up the torch and continue the commercialization of microtube heat exchangers and other component and system-level thermal management innovations. The future is here and innovation is no longer optional. Long live the spirit of innovation that Reaction Engines embodied from start to finish.