2023-10-25
A brief introduction to heat sinks in aerospace and electric vehicles
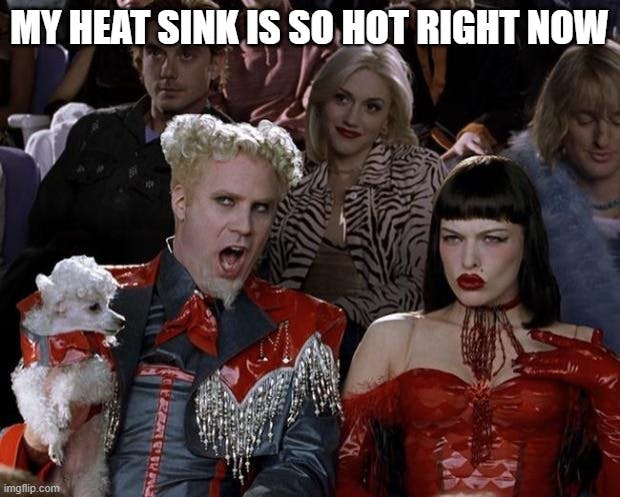
Blog
What comes to mind when you hear the term “heat sinks”? No, we’re not talking about your grandma’s kitchen sink full of scalding hot dishwater. And, for you fellow fans of spoonerisms, we’re not talking about heat seats, seat kinks, hinks seats, or even skink feet. We’re talking about heat sinks, which absorb and disperse heat by direct contact with a hot object, and are the most basic and most widely used type of thermal management device. If you’ve got excess heat within a system, the simplest place to start is by adding a heat sink.
However, though heat sinks can be stone-axe simple in some cases, they can also be quite complicated, depending on the type and application. Let’s go over some of the basics of heat sinks, particularly as they apply to aviation and aerospace.
Heat sinks in electronics and aerospace avionics
Heat sinks are commonly found in modern electronics and anything with computing power. Inside a desktop PC, laptop, or pretty much anything with a computer processor in it, you’ll find heatsinks on the CPU, motherboard, graphics card (if applicable), and inside the power supply. Any processor or electronic device that generates heat (and they all do) will utilize a heat sink.
Heat sinks are vital for removing heat from electronic components and extending their service life.
Common types of heat sinks in electronics
There are several different styles of heat sinks, and they are utilized in different applications according to price, size, and the amount of heat being generated. Let’s go over a few.
- Heat spreader: This is the simplest type of heat sink used in electronics, and is basically a flat piece of metal connected to a processor or motherboard. It may not even be recognizable as a heat sink, as it might be branded and can appear to simply be a thick decal. But the heat spreader serves an important purpose, drawing heat away from electronic components so it can radiate off of the larger surface of this type of heat sink.
- Passive, finned or pinned heat sinks: These are the next step up from a basic heat spreader, and include the addition of vertical fins (which are often segmented into pins or posts) to increase the amount of surface area and mass to shed heat more efficiently. The downside of this type of heat sink is increased manufacturing cost (due to the increase in complexity of the design as well as more metal) and greater size, which can create packaging problems (particularly in an aerospace application where efficient use of space is always a primary consideration).
- Finned heat sinks with axial fan cooling: These are very common in personal computers as well as in aerospace and military applications. This is basically a robust, finned heat sink with the addition of an axial fan directly on top of the structure, blowing air across/through the finned area. This greatly increases the efficiency of the heat sink with only a minor increase in size and weight. Electrical draw is increased, but the tradeoff is almost always worth it due to the improved performance and longevity of the device being cooled. Naturally, whenever a fan is employed, you must take “downwind” components into consideration, as that heat will be flowing from the heat sink to other areas of the system.
- Heat pipe/vapor chamber heat sink: Powerful computers and electronics may need this type of heat sink, at an increased cost. A heat pipe is the simplest type of this device, and is basically one or more closed pipes filled with a phase-changing liquid, and a “wick” along one side allowing cooled liquid to return to the hot spot. As the device heats, the liquid is changed into a gas, which moves along the pipe to the other/cool end, usually equipped with radiator fins. As the gas cools, it condenses back into a liquid, which travels back along the wick to the hot spot, and the cycle repeats.
The vapor chamber heat sink or heat pipe is connected to the hottest part of the device, typically a CPU or graphics card in a PC, laptop, or avionics system, and is constructed of small pipes (usually copper) containing a liquid or gas that is constantly changing phases as the material is cycled through the system. - Liquid cooled systems: Liquid cooling is becoming more common in powerful computers and processors, as water or coolant is very efficient at shedding heat. The coolant is pumped through the passages of a “water block” or thermal block connected to the main heat exchanger or heat sink, and takes excess heat away to a radiator system, typically cooled by axial fans. More advanced systems may utilize microtube heat exchangers.
In each of these systems, thermal paste is commonly used between the hot item itself and the thermal block, heat spreader, or heat sink. Thermal paste (also called thermal compound) is applied to fill in any microscopic air gaps between, say, a CPU and a heat sink. This increases the efficiency of the heat transfer. Thermal paste is typically carbon or metal particles suspended in an epoxy, silicone, acrylate, or urethane base.
Advancements in heat sink technology for aerospace and EV applications
The simplest form of heat sink is the passive heat sink, which derives its capability through sheer mass. The more mass something has, the longer it takes to heat up (or cool down). A huge, thermally stable heat sink buried in the Moon’s or Mars’s surface is one of the ways planned for long-term outposts to support off-earth exploration, including the Artemis missions. Rock and earth makes a passable insulator, and in the temperature extremes found on the Moon and Mars, a permanent outpost structure will need to rely on a high-mass, buried heat sink to stabilize temperatures and efficiently heat or cool the habitable space within any buildings.
(As an example of how even materials such as concrete and asphalt can act as heat sinks, visit the Phoenix metro area in the middle of summer. The urban sprawl soaks up the sun’s rays all day, and then gradually releases all that heat during the night. It’s quite common to see air temperatures above 100°F/37.7°C at one o’clock in the morning within city limits.)
However, when it comes to things that fly, “high mass” and “huge” are generally not terms conducive to success. So there is an ongoing search for more efficient heat sinks to enable thermal management for aerospace applications, particularly in the new fully electric eVTOLs or air taxis. As the world moves more fully toward solar farms and fully electric vehicles, there is an increased need for super-efficient heat exchangers and heat sinks that can shed lots and lots of heat, but in light, small packaging constraints.
One of the latest trends, especially in eVTOLs and high-powered lasers for directed energy weapons, is toward double-layer microchannel heat sinks (DLMCHS). As you might imagine, these heat sinks are arranged in two layers, with small, usually rectangular passages, and the whole affair rather resembles a 2-story apartment building. Compared to the single-layer design, the updated style “improves the uniformity of temperature distribution on the heat sink when the counter-current flow is used, and saves the pumping power by up to 60%,” according to one source. Additionally, the double-layer design offers improved heat dissipation capability due to increased heat transfer surface area, increased heat transfer coefficient, and enhanced thermal stability by dissipating heat more evenly and preventing hot spots from forming.
One recent study proposes an innovative design for improving double-layered microchannel heat sinks further, combining wavy microchannels with porous vertical ribs within the heat sink. The superiority of the new design has been demonstrated by comparing it with three existing double-layered heat sink designs under constant pumping power constraints. Compared to the three existing designs (straight microchannels and solid ribs; straight microchannels and porous ribs; wavy microchannels and solid ribs), the analysis showed that the porous-rib, wavy microchannel design reduced the pressure drop across heat sinks, inducing Dean vortices and enhancing coolant mixing.
Another new study extols the double-layer micro-jet heat sink (DLMJHS), which is a very recent development stemming from a need to reduce heat in the motor inverters in electric vehicles. This new approach, still in the development phase, involves introducing micro-jets of liquid coolant into a double-layer heat sink, in a specific process called “impingement.” “Compared to the traditional cooling approaches, it was found that the output power of the inverter underwent a significant enhancement by implementing the micro-jet impingement technique. Moreover… with constant power output, the inverter’s temperature tremendously reduces by using the micro-jet method. [The study] also revealed that jet impingement decreases the non-uniformity of the temperature distribution, enhancing the device’s reliability.”
We are fascinated by the process of innovation in all aspects of thermal management. When one component of a system is significantly improved, it often allows previously unimaginable improvements in other aspects of a system. As just one example, think of the drastic breakthroughs in aviation and aerospace made possible by the development of high-performance composites and superalloys. The impact is gargantuan. We’re excited to see how developing heat-sink technologies might be incorporated into larger environmental control systems or other thermal management applications in aerospace.
–By Jeff Davis, Intergalactic Scribe
Sources:
https://www.sciencedirect.com/science/article/abs/pii/S1359431123008657
https://www.sciencedirect.com/science/article/abs/pii/S1359431122004112
https://link.springer.com/article/10.1007/s10973-020-09317-3
https://www.nature.com/articles/s41598-022-23061-8
https://www.tandfonline.com/doi/abs/10.1080/01457632.2022.2148346