C-130 Hercules: Lockheed’s do-everything transport in continual production since 1956
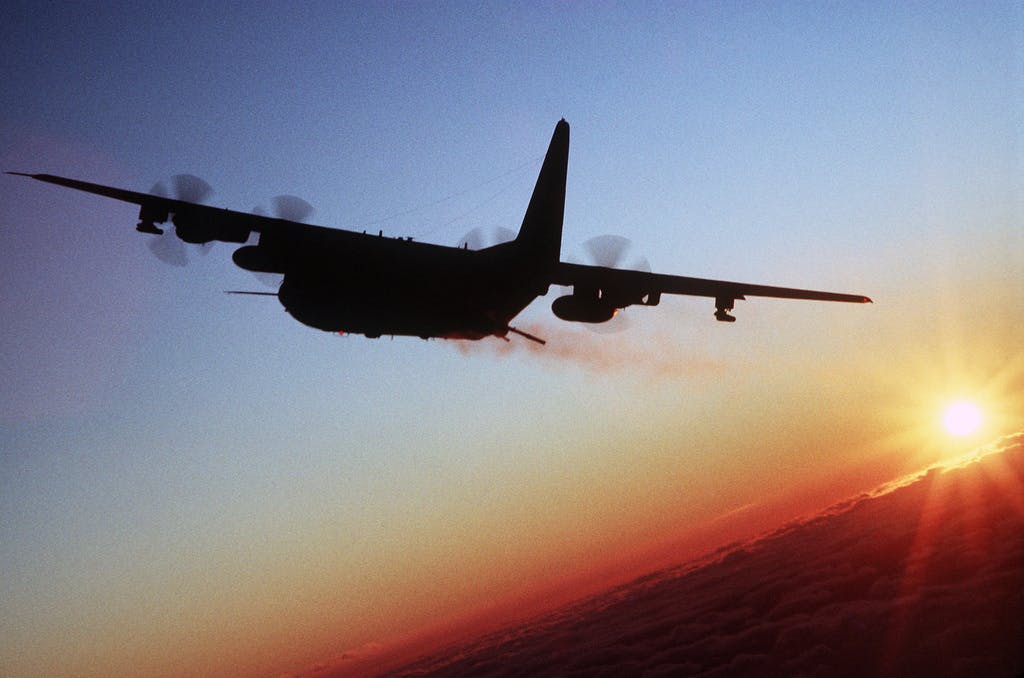
Blog
We’ve talked about the venerable B-52 bomber that’s still in active service, first flying in 1954, and wondered at its longevity and enduring battlefield relevance. However, the last B-52 rolled off the assembly line way back in 1962. So, while all currently flying Stratofortresses have been upgraded and improved over the years, they're still 1960s-vintage airframes. Lockheed’s C-130 Hercules, on the other hand, is still being built today. There’s no other military aircraft with a production track record as long as the C-130, which has been in continual production since 1956, longer than any other military aircraft on earth.
What makes the C-130 Hercules so good?
So, how has the remarkable C-130 survived for nearly 8 decades while so many other designs have been relegated to the airplane boneyard? The name of the game here is multitasking. In the increasingly specialized world of aerospace, there’s real value in a durable, capable aircraft that can fill multiple, diverse roles in both military and commercial markets. There’s also a lot to be said for getting the fundamental design and engineering right the first time.
The C-130 was conceived and developed in the early 1950s as medium-heavy strategic airlifter and troop transport, with the prototype first flying in 1954 and the first production aircraft delivered to the US Air Force in 1956. However, over the years, its versatility, durability, and easy flying characteristics have allowed C-130s to flex into multiple additional duties, including tactical gunship (in the famous Vietnam-era AC-130 configuration), search and rescue, firefighter/firebomber, weather research/hurricane chaser, aeromedical missions, aerial refueling, arctic resupply, airborne early warning, photographic and electronic intelligence, and natural disaster relief, just to name a few. Over 2,500 C-130s have been made and delivered to 63 nations, in 70 distinct variants (think about that!).
Another key factor for any long-serving military aircraft, including the B-52, F-16 Fighting Falcon, F/A-18 Super Hornet, and F-15 Eagle, is the ability to accept rolling upgrades. If the basic airframe and design is sound, upgrades to the engines, controls, avionics, weapons systems, radar, and communication systems can be made as they develop. The C-130 has had multiple updates to its turboprop engines, propellers, electronics, hydraulics, fuel capacity, and all tactical systems over the decades, which helps keep this 1950s design relevant on today’s battlefields and civilian markets.
The C-130 was not the largest aircraft in the USAF’s fleet in 1956 (not by a long shot), but its 97.5 foot length and 132.5 foot wingspan (29.1 m and 40.38 m, respectively) look positively cute next to something like the C-5 Galaxy’s 247 foot length and 222.5 foot wingspan (75.2 m and 67.8 m, respectively). However, the C-5 can carry 6 times the payload. Despite this, many commanders find the C-130 superior to “more modern” jet-powered tactical transport aircraft in many situations.
Advantages of the “Goldilocks” sized C-130 and its turboprop engines
Total carrying capacity isn’t everything that needs to be considered for a strategic transport fleet. For example, the takeoff distance at a normal maximum takeoff weight of 155,000 pounds (70,305 kg) is 3,290 ft (1,003 m) for the C-130J model and 3,586 feet (1,093 m) for the C-130H model. Depending on which source you read, using maximum effort methods and a lighter load, both takeoff and landing distances required for the C-130 range from “less than a thousand feet” (304 m) to 1,800 feet (548 m). For comparison, the takeoff distance required by a 747 airliner/transport aircraft is between 7,500 and 10,000 feet (2,286-3,048 m). The C-5 Galaxy’s takeoff and landing distance requirements at maximum-load gross weight are 8,300 feet (2,500 m) and 4,900 feet (1,500 m), respectively.
Operating out of remote, forward areas is also the C-130’s bread and butter. When employing all its capabilities and tools, the C-130 can fly in and out of unimproved dirt airstrips that measure just 3000 feet long by 50 feet wide (or shorter, depending on payload). For comparison, a similar-sized commercial jet airliner (or similar-sized military jet transport) requires a paved runway that is at least 6000 feet long and 150 feet wide. The Hercules can also land on and take off from a sandy beach.
Additionally, the propeller-driven Hercules is less susceptible to the swirling debris and other airborne objects that come into play when landing or taking off from unimproved surfaces. A jet-powered heavy transport aircraft like the USAF’s C-17 Globemaster III can take off and land on runways as short as 3,500 feet (1,064 meters) and 90 feet wide (27.4 meters), as well as on smooth dirt surfaces. However, due to the increased risk to the engines from object strikes or debris, the Hercules is often considered superior in truly rough forward areas, despite its much smaller size and carrying capacity compared to the modern heavy transport jets.
The C-130’s capabilities at surviving extreme conditions and wicked updrafts is evident by its use as a weather reconnaissance aircraft, or “hurricane hunter.” Specially equipped C-130s are flown intentionally into hurricanes, through the eye, and then out the other side, repeatedly, to help map the speed, size, and path of these destructive storms. This kind of punishment would send many lesser aircraft to the ground in pieces, but the Hercules eats it up and asks for more. On the other side of the temperature spectrum, firebomber variants of the Hercules have to endure extreme heat and violent up/downdrafts that can rip the wings off normal aircraft, but the C-130 handles it with aplomb.
As a final point in the C-130’s favor, it costs around $10,000-$15,000 per hour to operate the Hercules. The C-17 Globemaster III? About $24,000/hr. The C-5 Galaxy, on the other hand, costs over $100,000 per hour. Cha-ching.
Need more evidence of the C-130 Hercules’s badassery? It can do a frickin’ LOOP.
USAF plans to fly the C-130 into the 2030s and beyond
The C-130 has been threatened with retirement and replacement several times, as you can imagine for an airframe design that’s been in continual use and production since the Eisenhower administration. But updates and upgrades, along with a rapidly shifting military budget, have kept it in the fight. Currently the Air Force is conducting a rolling upgrade of existing C-130H models to electric propeller control systems rather than the legacy hydraulic systems, resulting in improved response and performance during rapid throttle movements. However, all currently manufactured Hercules aircraft are of the C-130J Super Hercules variant. Over 500 C-130J aircraft have been delivered to 26 operators in 22 countries. The unit flyaway cost of the C-130J was just over $67 million in FY2016, or around $87 million in today’s dollars. If you want the AC-130J Ghostrider gunship, it’ll be a significant upcharge, at $165 million per copy.
The C-130J Super Hercules aircraft in current production benefits from all of the previous decades of improvements and upgrades, and is more capable than ever. This is most notable in the cockpit, where dual HUD (heads-up display) screens hang from the top of the cabin to allow see-through information gathering by both pilots. A single, computer-assisted power-control (auto-throttle) system manages the output of all four engines, greatly simplifying the pilot’s tasks during busy takeoffs and landings. Other avionics feature modern, multi-function displays, multi-color radar, a digital moving map, Link-16 tactical datalink, Terrain Awareness and Warning System (TAWS), Ground Collision Avoidance System (GCAS), and Traffic Alert and Collision Avoidance System (TCAS). The upgrades to the avionics and flight systems mean that the minimum crew required has been reduced from 5 to just 3 people: 2 pilot/copilots and a loadmaster. The Navigator and Flight Engineer spots are no longer necessary, saving money, resources, and manpower.
The “stretched” version of the C-130J-30 provides a full 55 feet of cargo compartment length, 15 feet longer than the original C-130 transport aircraft. The space is provided by inserting a 100-inch forward and an 80-inch aft plug to the fuselage. This longer, 112 feet 9 inch (34.69 m) fuselage length results in 30 percent more usable volume for increased seating, litters, pallets, or airdrop platforms. The updated aircraft can transport 128 ground troops (previously 92), 92 paratroops (previously 64), 97 litters in aeromed configuration (previously 74), or 8 463L master pallets (previously 6).
The C-130J’s powerplants have been upgraded to 4 Rolls-Royce AE 2100D3 turboprop engines producing 4,591 shaft horsepower each, spinning fully composite Dowty R391 6-blade propellers. C&S Propeller points out the “swept-back design with ARA-D/A airfoils, with individual blades constructed of glass and carbon fiber with an inner core of polyurethane foam. A single lever manages the electronic prop control system, which is also integrated with the engine controls, providing simplified operation. This, along with other design features, makes the system very lightweight while delivering good takeoff and climb performance, as well as low levels of noise.”
The increased performance of the new engines combined with the latest propeller technology and increased room for cargo boosts the C-130J’s versatility even further than its already well-earned reputation holds.
Lockheed Martin says, “In addition to the significant increases in operational capability and performance, the C-130J offers a greater value when compared to any other tactical airlifter: System reliability and maintainability are improved by up to 50 percent; maintenance man-hours per flight hour are decreased by up to 68 percent; and flight and maintenance manpower are reduced by up to 50 percent, resulting in a 47 percent lower squadron operating and support cost.” All good things.
That’s fine, but what about the C-130’s environmental control system (ECS)?
As aerospace and ECS geeks, we are always interested to see how different aircrafts perform as far as their environmental control systems go. The C-130’s ECS is capable of lowering the cockpit environment from a heat-soak temperature condition at an external ambient temperature of 120°F (49°C) down to 84°F (28.8°C) within 30 minutes from the start of ECS cooling operation. Anyone who has sat on the tarmac in Iraq or Afghanistan in the summer knows that’s pretty impressive. Conversely, if you’re flying glorified TV dinners to a luxury adventure tourism group in Antarctica, the C-130’s ECS is capable of increasing the cabin’s average temperature from -22°F (-30°C) to 41°F (5°C) within 20 minutes. Plus, cargo-floor heating is accomplished by circulating hot engine bleed air through an underfloor manifold. Cooling for the avionics, flight-station displays, and rack-mounted electrical equipment is provided using a forced-air cooling system.
Interestingly, when Lockheed first upgraded the engines from the Allison T56 to the new AE 2100 series in 1996, test pilots discovered that the change in aerodynamics led to an increased tendency to roll and stall at lower speeds. Lockheed tried multiple aerodynamic solutions without success, and ended up adding an automatic stall-prevention “stick-pusher” control device that would override a pilot who was ignoring visual and audible stall warnings.
Additionally, Lockheed discovered that some directional/control problems were being caused by ice buildup on the tail control surfaces. Because the newer engines were more fuel-efficient, they no longer produced sufficient bleed air to continuously warm the tail surfaces. Engineers had anticipated this problem, but even so, the cyclic system that replaced the old de-icing system was found to be insufficient when the C-130J flew in extreme conditions. Lockheed had to extend the new de-icing system higher and lower than before on the vertical stabilizer to prevent ice formation. This added more delays to an already overdue delivery schedule, and resulted in Lockheed Martin exceeding its initial C-130J development budget of $300 million. By the time the C-130J was ready for prime time in September 1998, Lockheed had spent over $900 million in development costs alone.
Now, we’re not saying that a few lightweight, compact, super-efficient microtube heat exchangers could have saved Lockheed Martin almost a third of a billion dollars… but we’re not not saying it, either.
–By Jeff Davis, Intergalactic Scribe
Sources:
https://www.af.mil/About-Us/Fact-Sheets/Display/Article/1555054/c-130-hercules/
https://www.lockheedmartin.com/en-us/products/c130.html
https://cspropeller.com/2016/09/21/54h60-vs-dowty-r391/
https://www.af.mil/About-Us/Fact-Sheets/Display/Article/467756/ac-130j-ghostrider/
https://www.businessinsider.com/air-force-plane-cost-per-flight-hour-chart-2016-3
https://sofrep.com/fightersweep/maximum-effort-landings-in-the-c-130/
https://youtu.be/h9S0acPBRTE?si=V5Xaj__cIHzT4yEc
https://en.wikipedia.org/wiki/Lockheed_Martin_C-130J_Super_Hercules