Cold plates and conductive cooling: a brief overview
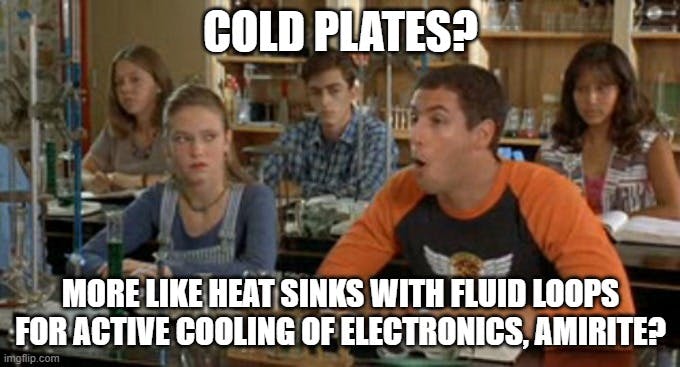
Blog
Cold plates are nice when you’re eating a particularly delicious salade niçoise or super-fancy $100 shrimp cocktail. However, chilled dinnerware is not what we’re talking about in this context. So finish your appetizer and let’s talk about cold plates as a form of conductive cooling for computing, high-voltage electronics, electric vehicles, and other applications, including aerospace.
What is a cold plate and how does it work?
A cold plate is in its most basic form a metal block, usually made of aluminum or copper (both of which are known for transferring heat very efficiently), through which a simple series of loops of tubing runs. The cold plate is attached directly to a hot object in need of cooling (thermal paste may be used, or the connection may be purely mechanical). A cooling liquid is circulated through the internal tubes (typically copper, stainless steel, or a corrosion-resistant alloy). The cooling liquid is part of a closed loop system designed to transfer heat from the device you wish to cool to the liquid, which is then circulated through a remote heat exchanger. There, the heat dissipates into the ambient air environment, or is removed more proactively by a secondary cooling system.
There have recently been advances in multi-axis CNC machining or additive manufacturing (3D printing) methods for making tubeless cold plates with integral internal passageways or microchannels, rather than simple loops of tubing, which decreases thermal resistance and improves heat transfer to the cooling liquid.
Since cold plates transfer heat from hot objects via direct contact of the metal plate, they are correctly termed conductive cooling devices. However, since they also utilize circulating fluid to shed heat from the internal surfaces of the metal plate block, they could also be termed convective cooling devices.
What types of cooling liquids are used in conjunction with cold plates?
The most common liquids used in closed-loop cold-plate cooling systems are water, an inhibited glycol/water mix, dielectric fluids (typically made from one or more low-viscosity, highly pure synthetic oils), and specific heat-transfer fluids custom-designed for a particular application. However, in some industrial and aerospace applications, such as the International Space Station, liquid ammonia is used.
Nanofluids are also increasingly being used in some cold-plate systems. The presence of (typically metallic) nanoparticles in nanofluids increases the surface area and contributes to better flow during liquid mixing, higher thermal conductivity, and improved heat transfer coefficient. The tradeoff is typically increased viscosity compared to conventional cooling fluids, which requires more pumping force to circulate the fluid through the system. However the improved thermal performance is worth it in some applications.
Is a cold plate the same as a heat sink?
Cold plates and heat sinks are similar in that they are typically constructed out of a block of metal that is placed in direct contact with the device or item you wish to cool. However, as we explain in our full article about heat sinks, the more basic forms of heat sinks are passive thermal management devices and can be as simple as a heat spreader (a block of metal to help disperse and radiate heat) or a finned design that radiates heat more efficiently to the ambient air environment. On the other hand, a cold plate, while also a block of metal that absorbs heat from a device, is not a passive cooling device since it also includes tubing or passages filled with fluid, and an externally powered cooling pump that cycles the cooling liquid through the cold plate and at least one remote heat exchanger.
Since closed-loop cold-plate systems require the input of energy to cycle the cooling liquid and thus cool the device (at the minimum a fluid pump of some type is used), they are technically not passive thermal management systems, but rather active thermal management systems.
Where are cold plates used?
Cold plates are widely used in power electronics (high-voltage applications), conventional electronics, computers, server towers, IGBT power modules, automotive applications (particularly electric vehicles), wind turbines, lasers (including directed energy weapons), and aerospace applications such as cooling eVTOL/UAV battery packs, electric motors, and avionics.
Larger, more low-tech cold plates are also a very common way soda fountain drinks are cooled, only in this case, the liquid being cooled by circulating through the tubes in a large aluminum cold plate is the soda water and beverage syrup product itself. These cold plates can be cooled by refrigeration, but are most efficient when they are simply immersed in ice. When you go back for a refill of your 44-ounce Diet Dr. Pepper, chances are you’re making use of a cold plate system.
What are the advantages of cold plate cooling systems?
First, liquid cooling using cold plates is significantly more effective than air cooling. Heat transfer by air is limited. To dissipate large amounts of heat by air, a large mass flow rate is required (because heat transfer capacity is limited by the density of the fluid–in this case, air… which isn’t very dense at all, unlike your brother-in-law). As liquid is denser than air, liquid cooling is able to achieve better heat transfer at much lower mass flow rates.
Cold-plate liquid cooling also allows reductions in the weight and size of powerful electronics, which is important for mobile, military, and/or airborne systems where size and weight are primary concerns. Liquid cooling also allows for increased performance of electronics and any system where excited electrons are used to perform work. More powerful batteries and motors for your Tesla nickel mine excavator means more heat is generated, which requires more powerful cooling systems. When lots of heat is being generated, liquid cooling is where it’s at.
Additionally, since heat is removed directly from a hot object by direct contact/conduction in this system, that object itself doesn’t need to be exposed to the cooling liquid. Delicate electronic components typically don’t do well in watery environments, with some exceptions.
Furthermore, since the heat exchanger in a closed-loop cold-plate cooling system is remote, you can locate that heat exchanger as far away as you like, directing or “exhausting” that heat wherever you want. You can even use it to warm up another part of a larger unit if desired, increasing efficiency.
Downsides or caveats for cold plate cooling systems
While the cold plate and heat exchanger setup is effective at reducing the size and weight of the electronics themselves, you also have to factor in the size, weight, and complexity of the cold plate, piping or tubing, and at least one heat exchanger, if not two. Additionally, depending on the capacity and size of the system, you may also require a decompression tank (as fluid temperature changes, pressure changes). Soon, the system can become quite complicated compared to some more simple heat-sink systems.
Additionally, utilizing cooling liquid means using tubing and piping and joints and connectors and fittings and flare washers and possibly brazing. This complexity increases the risk of leaks, corrosion, and the associated damage they can cause to nearby systems. Water is very efficient at removing heat, but it also freezes at relatively high temperatures and boils at relatively low temperatures. Glycol additives can improve these ranges, but they also lower water’s heat-shedding capability. Ammonia is extremely corrosive, and exposure to high concentrations of ammonia in air causes immediate burning of the eyes, nose, throat, and respiratory tract, and can result in blindness, lung damage, or death. Super fun!
Since heat exchangers and cold plates themselves rely on internal passages for efficient fluid flow, keeping these passages free of corrosion, debris, and blockages is paramount. Heat exchangers may or may not be serviceable, depending on their design, but most cold plates’ internal passages are either permanently milled/printed or rely on internal metal tubing that can’t be replaced if it becomes damaged or blocked. Thus, regular maintenance and inspection of the system is required, which adds cost and staff hours.
However, the greatly improved thermal performance of cold-plate/heat-exchanger cooling systems compared to even the more advanced passive heat sinks means cold plates are here to stay. Don’t forget to chill the salad forks!
–By Jeff Davis, Intergalactic Scribe
Sources:
https://www.nasa.gov/wp-content/uploads/2021/02/473486main_iss_atcs_overview.pdf
https://youtu.be/G6Ys4qQuYPw?si=_km9aLVu_qWItte2
https://www.compelma.com/en/the-what-why-and-how-of-cold-plates-for-thermal-management-compelma