Introducing GS1-EV Eagle5, the first thermal management system developed specifically for eVTOL and electric aircraft
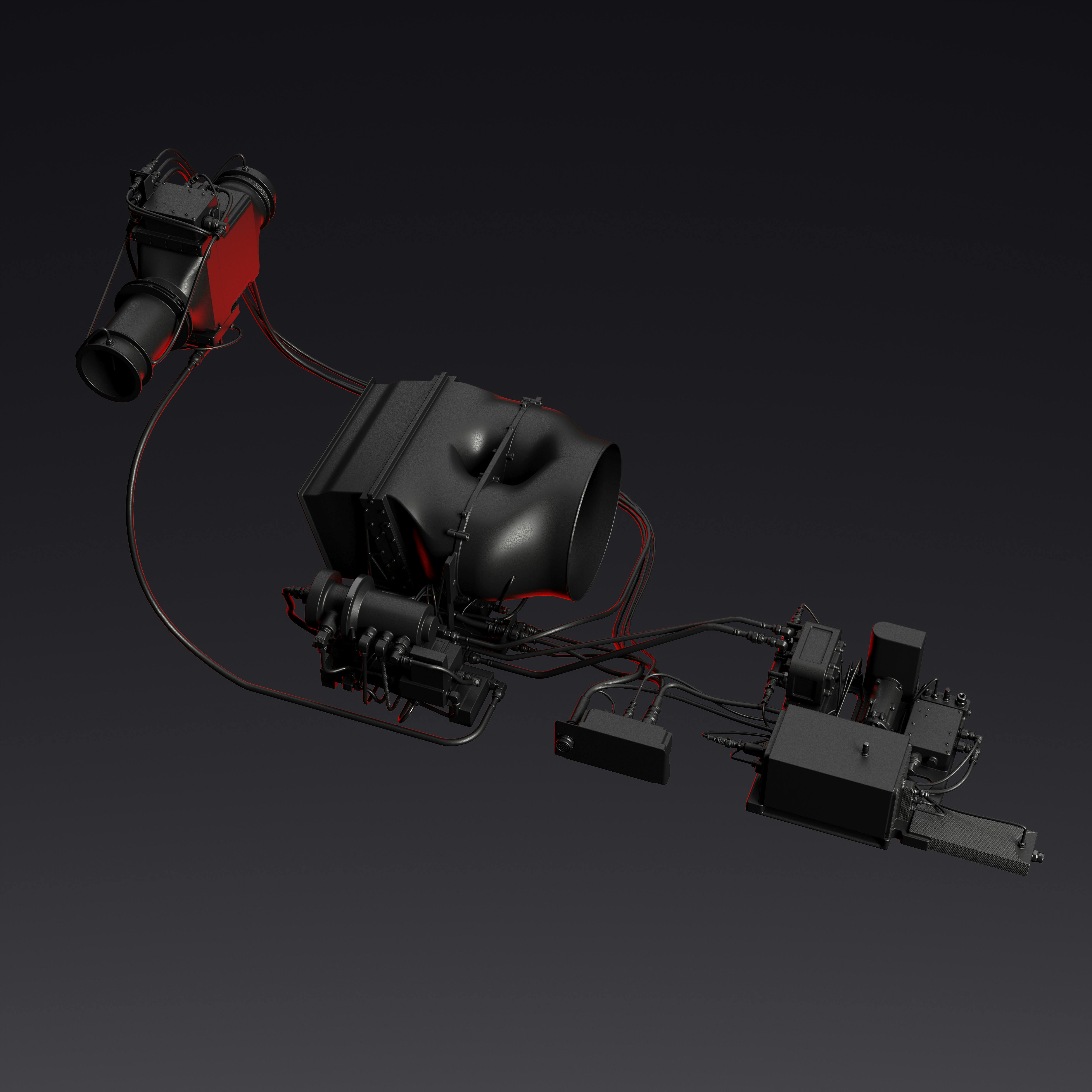
Blog
We’ve mused before about how the 80s and 90s were the golden years of pop culture because the future seemed so rife with insane and inspiring possibilities. It makes sense. The U.S. was coming off perhaps the most concentrated period of technological innovation in human history, punctuated by Apollo 11 astronauts putting boots on the moon a mere 66 years after the Wright Brothers’ maiden flight. But instead of expanding further into space, we put the lunar program on moth balls and entered a period where progress came in inches instead of giant leaps.
Against that backdrop, it makes sense that the last two decades of the 20th century were rife with futuristic themes in art, music, movies, and television. This is the era that gave us Star Wars, Back to the Future, and yes, Howard the Duck.
Speaking of Back to the Future, we were promised flying cars by 2015. What happened? Well, turns out Marty McFly and Doc Brown were only off by about a decade. We won’t have flying DeLoreans, but by 2025 we should have the first commercial “air taxis” (the industry lingo is eVTOL, short for electric vertical takeoff and landing) buzzing passengers around in huge, electric drones. We wrote a whole thing about air taxis, and you should know that the smart folks at Morgan Stanley expect the eVTOL market to grow to $1 trillion by 2040 and NINE TRILLION DOLLARS by 2050!
The thing is these sweet flying taxis need to keep the electronics, passengers, and electric batteries cool to operate properly. So, guess what? We’re launching a new product.
Check out GS1-EV Eagle5, a combined ECS-BTMS for eVTOL (holy acronym overload!)
How’s that for alphabet soup? Hang with us and we’ll break down all the acronyms.
We’ve already explained that eVTOL is a flying taxi. If you want air conditioning or heating while you cruise, you need an ECS (environmental control system). And if you don’t want the electric batteries that power the air taxi to catch fire (!!), you need a BTMS (battery thermal management system). Eagle5 is a combined ECS-BTMS for eVTOL. Mic drop.
Now that we have our acronyms in order, let’s take a gander at the Eagle5. It’s the first off-the-shelf thermal management system designed specifically for eVTOL and electric aircraft. It uses a pretty sweet two-phase system that we’ve developed at Intergalactic – more on this below, but suffice to say it allows us to cover a wide range of cooling and heating needs while keeping weight and size to a minimum. Eagle5 also pulls in a bunch of qualified hardware that we’ve put through a battery of brutal tests.
You can read more about Eagle5’s specs on our product page and in our very official press release, but in summary, it’s:
- Lightweight
- Compact
- Scales up or down and can accommodate even larger regional electric aircraft
- Is intelligent, not analog, so it can efficiently handle variable thermal conditions
What is the pumped two-phase design, and how does it solve thermal problems unique to eVTOL and electric flight?
We’re so glad you asked! The short answer is we know electric aircraft need to solve two inverted problems: regulating variable temperature concerns with high spikes and doing so with a compact and lightweight thermal management system.
This is where our pumped two-phase architecture becomes super helpful. We’re going to hand the keyboard to Andy Kerlin, Director of Extra Super Hyper, Intergalactic’s internal R&D division which created Eagle5, to tell you in the words of an engineer exactly how it works. It’s a story of refrigerant loops, our patented microtube heat exchanger technology, and some wax. Are you sitting down?
From Andy:
A next generation thermal management system must be adopted by future competitive airframers to realize performance, range, and environmental needs in new, burgeoning markets. A new cooling system that has the potential to exceed these requirements leverages two subsystems in tandem to provide a holistic solution.
First, a subsystem that employs a phase change material heat exchanger, where an energy dense phase change material is used to absorb high transient heat loads and second, a complementary subsystem utilizing a pumped two-phase refrigerant cycle where liquid refrigerant is pumped to efficiently move heat, similar to other single-phase pumped liquid systems.
Both subsystems allow for a massive reduction in cooling system size, weight, and power draw. Cooling systems that utilize phase change materials in a thermal battery can be sized to nominal or average operating conditions instead of short duration, peak heat loads by simply absorbing these brief loads with the heat of fusion when melting and re-solidifying the phase changer material over time. Alternatively, a cooling system that is sized for worst-case peak heat loads may need to be several times larger and heavier to capture the corner cases that only account for 5% or less of flight time. The pumped 2-phase cycle uses a smaller pump at lower flow rates, reduced power consumption, and smaller piping by using liquid refrigerant that passes through a phase change, taking advantage of the latent heat of vaporization of the working fluid.
The phase change that occurs has the added benefit of maintaining near constant temperature for sensitive auxiliary components. In contrast, a single-phase cooling system, commonly found in automobiles and aircraft, only operates on sensible heat, and must rely on a much higher flow rate to remove the same amount of heat. That higher flow rate comes with a substantial penalty. It requires a larger pump that consumes more power and uses larger piping to keep pressures reasonable. In addition, the required liquid volume to fill traditional systems tips the scales in favor of a pumped 2-phase architecture. The benefits are stark: using a pumped 2-phase cycle over a traditional single-phase system reduces required mass flows by nearly an order of magnitude. This translates to significant savings in the overall mass and power budgets.
However, there are challenges that have kept this highly attractive system architecture at bay. If it was easy, it would’ve been done already! First, detailed analytical physics-based models must be developed to investigate initial use cases and cost/benefit analysis. Then, extensive empirical data must be generated from both the phase change heat exchanger and the pumped 2-phase subsystems. Lastly, this data informs and refines the analytical models by verifying performance across the operating envelope.
With validated, robust, data driven and correlated models, a system level optimization toolset can take into consideration a myriad of tradeoffs to confidently size and design appropriate equipment for specific platforms and applications. It’s essential to run and evaluate an entire pareto front of design outputs against specific application requirements and work with the customer on what they value. It’s also critical to effectively test and optimize virtually with a digital twin in conjunction with testing in the physical world. This approach greatly reduces time and cost for product development and ensures customer requirement compliance.
There are added complexities and smart digital controls that also need to be integrated in the overall system to ensure appropriate duty cycles of equipment and power draw for real-time heat loads. The system is designed to operate only at the level at which it needs to maintain thermal management goals. If there is an efficiency gain to be found that also leads to increased reliability with greater mean time before failure (MTBF), it’s identified and considered for the system.
Gone are the days of simple set points with parasitic bypasses that result in systems always operating at elevated levels, regardless of customer heat loads. Welcome to the digital age renaissance for aerospace thermal management systems (TMS). Goodbye (and good riddance) to outdated analog TMS that can’t keep up even if granted the space and weight they need to operate in.
Whoa, how neat is that?
In the not-too-distant future, you’re going to hail an air taxi the same way you hail an Uber, and you’re going to soar over those poor chumps sitting in traffic on the freeway. It’s the future Doc Brown promised, but even cooler thanks to Eagle5.
What’s with the name, Eagle5?
You might have noticed that we take an unconventional approach to naming our aerospace products and systems. We name our components after star constellations and our systems after 80s and 90s pop culture icons, with an emphasis on air and space – McFly, Starscream, Falkor, you get the idea.
We had a bunch of ideas for this product – maybe Interceptor, as an homage to Mad Max, Spinner, as a nod to Bladerunner, or Trimaxion, as tribute to the self-aware spaceship in Flight of the Navigator.
All worthy names, but we couldn’t stop thinking about the 1987 Mel Brooks classic, Spaceballs. The unlikely heroes of that particular film traversed the galaxy in a flying Winnebago called the Eagle 5, which happens to have our company name on its license plate. That felt like a sign. Also, our product naming convention lists the product series first (GS1, short for “great scott,” first generation), then a two or three letter shorthand for the product name. In this case, “Eagle5” translates into “EV,” which brings in the roman numeral for “5” and doubles as an acronym for “electric vehicle.” Kinda feels like this product name fell from heaven, folks. The gods hath smiled on us, indeed.
So, that’s how our innovative electric aircraft cooling machine got its name. Now you know.
How can I get my hands on that sweet, sweet two-phase thermal management system?
If you’re building an eVTOL or a larger electric aircraft for the commercial aviation or aerospace defense sectors, you might be tempted to inquire about this product. We don’t blame you! It can be modified and scaled up to satisfy a wide range of requirements. We think you should reach out. We don’t bite. (Well, Andy does, but we’ll keep him in the lab.)
If you’d like to talk, our engineers are all stretched out and ready to rock and roll. Just drop us an email at phonehome@ig.space. We look forward to hearing from you.