Active thermal management: A primer on forced air cooling
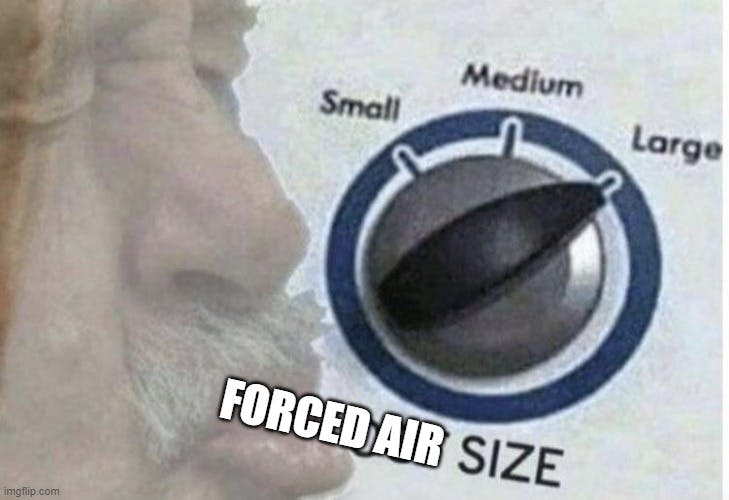
Blog
Picture yourself reclining on a linen divan on a sunny Caribbean beach, sipping an umbrella-laden beverage. Everything is almost perfect… except the sun is hot and the day is calm. You start to feel a little too warm. Now imagine, if you will, a generous soul gently fanning you to a comfortable temperature using a large palm frond. Ahhh… that’s better. This, friends, is the concept behind forced air cooling for aerospace and aviation, just on a more, um… fantastic scale. In short, just as your parents taught you when you had your first bowl of hot mush as a baby, blowing on something is the easiest and simplest way to cool it off.
Now imagine you need to cool off a steamy aerospace component, an e-vehicle battery, or an electronic device. You could hire someone to gently waft air toward it with her palm frond, or you could sit there and blow on it all day. Or, if you were smart and valued the use of your lungs, you could design a cooling system that utilizes the speed of an aircraft moving through the air and/or a powered fan to blow cool air on the device for you. That’s an active thermal management strategy called forced air cooling.
What is active vs. passive thermal management?
Active thermal management is a heat mitigation approach that requires external power to remove or redirect excess heat from a system. Some examples are vapor cycle systems, air cycle systems, thermoelectric coolers/Peltier devices, and closed-loop cold plate systems. The more basic forms of heat sinks, on the other hand, are passive thermal management devices and can be as simple as a heat spreader (a block of metal to help disperse and radiate heat) connected to an electronic component, or a finned design that radiates heat more efficiently to the ambient air environment.
Forced air and/or “ram-jet” cooling on aircraft is typically used in combination with heat sinks, cold plates, or vapor cycle systems, and requires either ram-air from the movement of the aircraft through the air (which obviously utilizes power) or, typically, axial fans to blow air over finned plates or heat exchangers, cooling them by convection. Since forced air cooling requires the use of external power to create “wind,” it’s an active thermal management strategy.
If you Google “forced air systems,” the vast majority of results will deal with commercial and residential HVAC heating systems, but that’s not what we’re talking about here. In this article we’re going to focus specifically on forced air cooling for aviation and aerospace components.
Forced air cooling in aviation and aerospace
Using natural or ram-air convection cooling has a long history in powered flight, right back to Orville and Wilbur. Using the speed of an aircraft or the rotation of propellers to “blow” cool air over hot metal engines and components was a widely used technique in the early decades of human aviation, and most privately flown piston-driven aircraft are still air-cooled to this day. In some cases, forced-air cooling is still used to prevent aircraft systems and electronics from overheating.
To improve efficiency, fins are frequently used in this type of system to increase the surface area exposed to the cooling air. Cooling fins are common on small aircraft engine cylinders, but are also commonly integrated into avionics housings, heat sinks, heat exchangers, and other heat-management components. The greater the hot surface area that can be exposed to cool airflow, the more heat can be removed from a system.
Depending on the design and application, cool air may be directed over hot components via intake cowlings or vents, or it may be drawn in or accelerated via axial fans or vacuum in forced-convection designs.
Benefits of forced-air cooling for aviation and aerospace
The primary benefits of forced- or natural-air convection thermal management systems is that they are simple, reliable, durable, and inexpensive. All of these are good attributes when we’re talking about things that fly, particularly with people aboard.
A properly designed, multi-finned heat sink placed in the airflow generated by the flight of a small aircraft may be sufficient to cool some electronics or other components, and will be almost totally maintenance-free for its service life. As you add fans and ducting to the system, it becomes more complicated, but compared to closed-loop vapor cycle systems or liquid cooling, forced-air cooling is much simpler and generally more reliable, as there are fewer components to fail.
Downsides of forced-air cooling in aerospace and aviation applications
The disadvantages of forced-air cooling, however, can outweigh the benefits (literally, in some cases). The main problem is that air—even fast-moving air—flowing over a surface can only remove so much heat. It is the simplest form of cooling, but it’s also arguably the least effective. Today’s modern high-performance avionics and lithium-ion batteries used in e-vehicles generate an awful lot of heat, and forced-air/convection thermal management systems are simply not up to the task in many cases.
Forced-air cooling may be more reliable, but to shed a sufficient amount of heat, the systems and heat sinks have to increase in size and weight to the point that it often defeats the purpose in an airborne application.
Another potential problem with a forced-air system is that introducing ambient air into the cockpit or passenger compartment may be undesirable in some harmful external environments.
Speaking of harmful external environments, when there is no air, like when you’re in space, you obviously can’t use outside air to cool a system. However, you can force air from within a habitable spacecraft or space station over hot electronics or avionics, simultaneously cooling the device and warming the air inside the craft, if desired. In spacecraft, however, it’s more common to use either thermoelectric cooling or liquid cooling/vapor cycle systems and heat sinks with the radiating fins or specially designed heat exchangers exposed to the cold of space, rather than using a forced-air-type cooling strategy on internal electronics.
Liquid- or vapor-cycle cooling is so much more efficient at removing heat that forced-air cooling is usually reserved for low-heat and/or non-critical applications today.
–By Jeff Davis, Intergalactic Scribe