A primer on fans and blowers in aerospace and aviation
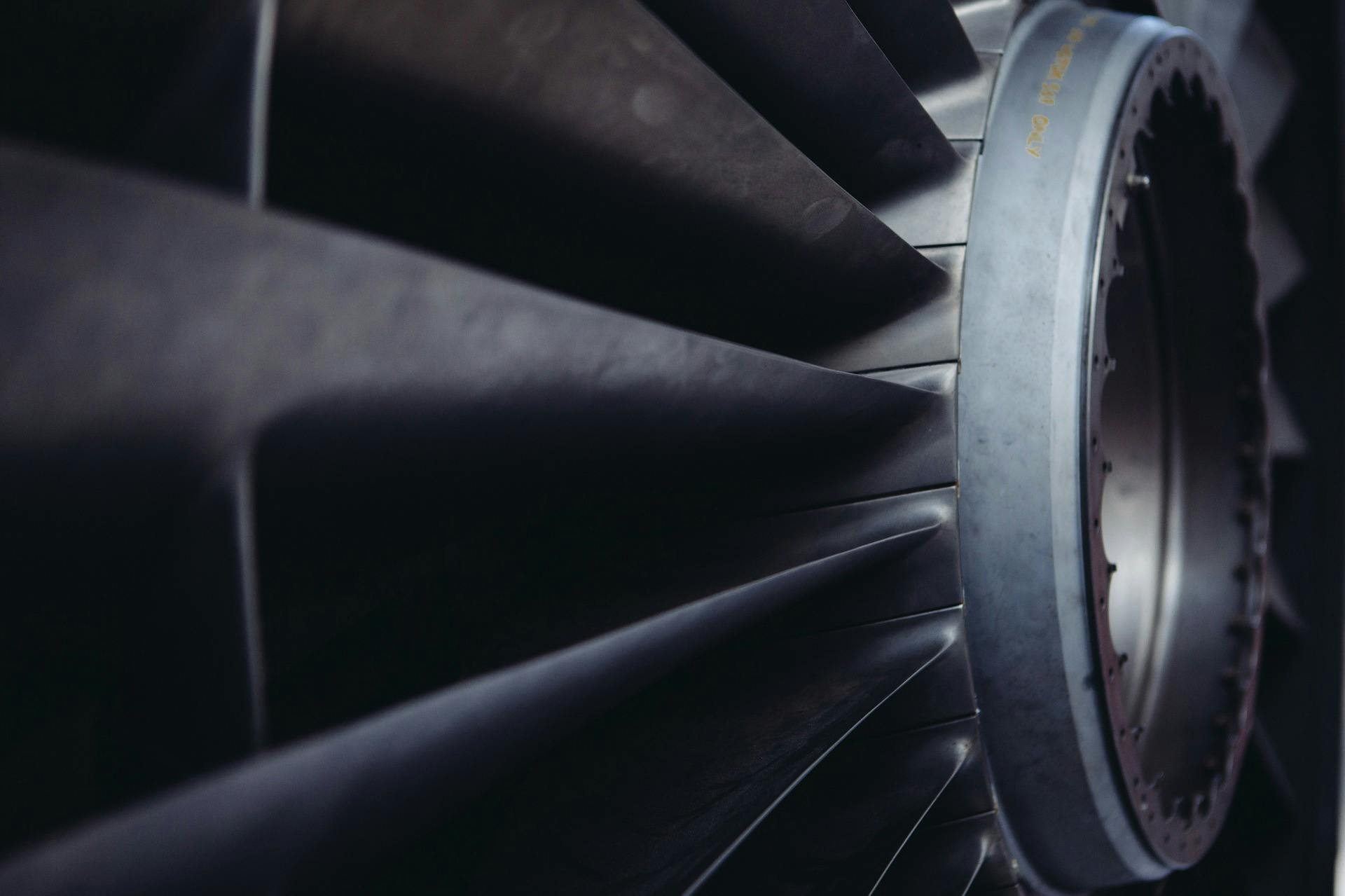
Blog
If you’re in aerospace or aviation, to keep hot stuff from getting too hot, you could just put your lips together and blow, but you’ll probably get better results (and Lauren Bacall won’t run the risk of hyperventilation) if you use an electric fan or blower. The most commonly used types used in aerospace and aviation are axial fans and centrifugal fans or blowers. Let’s go over the key features and uses of these vital components that keep systems working, aircraft flying, and people comfortable.
What’s the difference between axial and centrifugal fans or blowers?
Axial fans, commonly just called fans, are the simplest type of fan, and comprise a bladed propeller rotating on a central axis (hence the term “axial”), usually contained within an outer housing. Think of a common household box fan as an example. Centrifugal fans, commonly called blowers, are constructed of a hollow, barrel-shaped wheel or drum with impellers or vanes running along the longitudinal sides, and that wheel spins within a snail-shaped housing that uses centrifugal force combined with the internal shape of the housing to pressurize and redirect the airflow, which exits at 90 degrees perpendicular to the intake direction. A common household example is the portable “air mover” or carpet-drying type blower.
Fans and blowers are widely used in aerospace, aviation, and military applications, including (but not limited to):
- Engine cooling fans and systems
- Forced air cooling for aviation and aerospace components
- Gearbox cooling fans and systems
- Aerospace vapor cycle systems
- Pilot cooling systems/ECS for aircraft
- Avionics or other electronics cooling systems
- Electric propulsion systems and battery packs for eVTOLs and regional electric flight
- HVAC/air conditioning systems for buildings and structures
- Sand scavenge fans (often used on helicopters and armored fighting vehicles to prevent sand ingestion into the engine, avionics bays, or filters)
- Gunsmoke extraction fans (for rapid evacuation of potentially toxic gunpowder smoke from fighting vehicles)
How do fans and blowers work, and how are they different from each other?
Axial fans function in a linear fashion, where the intake and exhaust air is inline as it moves through the fan blades. Axial fans for aerospace and aviation almost always have a housing or orifice surrounding the outer edge of the fan blades to help improve efficiency. The orifice provides a determined direction for movement of the air and increases the velocity of the air. Without a housing or orifice, much of the air is pushed off of the sides of fan blades, rather than moving in an efficient, linear fashion.
Fans may be driven mechanically or electrically/digitally, but electrically driven fans are by far the most common today. Large industrial HVAC fans may utilize a central/axial mounted electrical motor driving the fan shaft, or they may be belt driven from an external motor. Small, efficient, electronically managed axial fans are integral to the performance of nearly all desktop and laptop computers, and are essential for removing heat from the high-powered electronics, avionics, and electrical power systems in today’s aerospace and aviation designs.
Fans may be set up as vane-axial, tube-axial, or simple propellers. Vane-axial and tube-axial fans are similar in that they employ close-fitting blades within a tubular housing. However, vane-axial fans have static guide vanes in the intake portion of the housing to guide and straighten airflow before it hits the fan blades. (Incidentally, if you’re looking for the best native high-voltage axial fan for military and aerospace applications, we know a guy.)
While axial fans’ airflow is linear, a blower’s design requires that air enter in one direction and leave moving in another direction. Like axial fans, blowers may be driven by either an integral electric motor or a belt connected to a separate motor. The motor spins the impeller wheel, and as the wheel spins, the vanes of the wheel combine with centrifugal force to draw air through the center of the wheel, pushing air outward through the vanes and into the housing, pressurizing it. The higher pressure and the “snail” shape of the housing accelerates the airflow, and the exhaust leaves the housing through an outlet at (usually) 90 degrees from the intake direction.
Blowers are often used in the evaporative stage of a typical HVAC air-conditioning cycle because blowers can overcome more static pressure than is possible using an axial fan.
In residential or commercial HVAC systems, large distribution blowers are commonly used both in the evaporative portion as well as the heat cycle when using a heat pump. In the latter case, the air is blown over the heat exchanger, or in the case of a heat pump, through the coil, and then moves the heated air through the structure. Smaller, draft-inducer blowers are also used within furnaces to facilitate proper combustion of heating fuels as well as the effective removal of harmful carbon monoxide that forms as a result of burning that fuel.
Axial fans are commonly employed in the condenser section of the cooling cycle, where a fan will blow through the condensing coils, removing heat that’s been absorbed into the refrigerant and distributing it outside of the system.
Advantages and disadvantages of blowers
Where static pressure is higher, or increased exit air velocity is desired, the larger, heavier blower is often employed. A common example is comparing the wind produced by a residential box fan to a carpet-drying blower or “air mover.” Compared to fans, blowers can deliver large volumes of air constantly, with minimal turbulence. They can also provide air at high static pressure, or operate in higher-pressure environments.
Due to their more robust housing and 90-degree inlet/output angles, it’s generally easier to modify a blower’s inlet and outlet geometry for integration with sub-systems, as well as incorporating non-return valves where necessary.
Some downsides of the blower are that they are commonly larger, heavier, and require more maintenance than axial fans. Large and heavy don’t often sell well in aerospace, so blowers are usually employed only when an axial fan wouldn't be able to do the required job efficiently. Blowers are also typically noisier than axial fans, and they lose efficiency when run at lower speeds.
Advantages and disadvantages of axial fans
Where static pressure is low, axial fans are more often employed, as they are often simpler, lighter, and smaller than blowers, and may require less maintenance and power to operate. Axial fans are often used in HVAC systems where pressure is not a concern and a lot of air movement is required. Axial fans are typically quieter than blowers, which can be a concern where stealth or aircrew comfort is a consideration.
A potentially important attribute of the axial fan setup is that it may be built to either blow or suck through an avionics zone, for example. In other words, a fan may sometimes be selectively used as both an intake or exhaust fan, running either forward or backward, depending on the conditions. Blowers are unidirectional since they depend on centrifugal force to build pressure and exhaust velocity.
Axial fans can be used in more compact spaces, which can be key in aviation and aerospace where every cubic centimeter of space is highly scrutinized. Downsides of axial fans are essentially that they usually don’t perform as well as blowers where high static pressure is involved. However, high-powered, high-efficiency axial fans are almost always the go-to in aviation and aerospace because of their relatively light weight, small size, simpler design, and reliability.
One very common use of fans in aviation is the high-bypass turbofan jet engine, which has grown to become the standard in commercial aviation over the past few decades. This type of jet engine has a large axial fan located in the intake portion of the cowling, driven by the same shaft that compresses the air-fuel mixture in the combustion chamber. However, much of the airflow driven by the large frontal fan isn’t directed into the jet engine chamber but rather around it, generating thrust without burning additional fuel. High-bypass turbofans have greatly improved the fuel efficiency and reduced the noise associated with traditional turbojet engines. Total thrust is reduced compared to a standard turbojet of similar size, but fuel efficiency is improved while maintaining sufficient thrust to weight ratio to keep the largest airliners and strategic transport planes flying.
Another increasingly popular use of (effectively) high-powered axial fans are the ducted fans or “electric jet engines” used today for low- or zero-emission aviation. But that’s a story for another day. Stay tuned!
–By Jeff Davis, Intergalactic Scribe
Sources:
https://beeindia.gov.in/sites/default/files/3Ch5.pdf
https://www.ametek-airtechnology.com/products/thermal-management-products/fansblowers