An overview of pumped two-phase thermal management systems
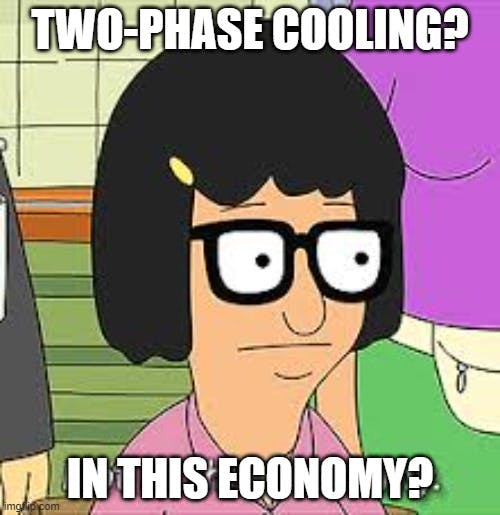
Blog
We’re betting you may not be familiar with Phase 2, a pioneer in graffiti art in the 1970s. Or, maybe you are. He is generally credited with creating the “bubble letter” style of graffiti writing, also known as “softies.” However, if you’re a hardcore thermal-management nerd, you might be familiar with pumped two-phase cooling systems, which have enabled huge leaps in electronic and heat-management performance in modern aerospace, aviation, and military applications. Awkward transitions aside, let’s look into the difference between single- and two-phase thermal management strategies and explain why these cool new systems are becoming essential.
How do single-phase pumped cooling systems work?
Pumped single-phase cooling systems are very common in internal combustion engined (ICE) automobiles, where a liquid coolant, typically ethylene glycol and/or water-based, is circulated through the hot engine cases by a water pump. That hot liquid, after absorbing heat from the engine, is circulated through the car’s radiator, which is just a large heat exchanger with loops of tubing and thousands of (usually) aluminum fins to dissipate heat as the cool air flows through. The cooled liquid is then pumped back into the engine, and the cycle continues as long as the engine is running and the water pump is turning. Liquid cooled ICE-powered aircraft were very common during World War II, and iconic fighter aircraft such as the P-51 Mustang, P-38 Lightning, Supermarine Spitfire, and Messerschmitt BF-109 all used liquid-cooled V-12 piston engines to achieve their amazing performance and speed. However, liquid-cooled aircraft engines are somewhat uncommon today.
Modern electronics using basic cold plates often operate on the same single-phase cooling principle. Cold plates are essentially metal blocks through which a simple series of loops of metal tubing runs. The cold plate is often attached directly to a hot electronic component in need of cooling (thermal paste may be used, or the connection may be purely mechanical). A cooling liquid (usually water, glycol, or dielectric fluid) is pumped through the internal tubes in a closed-loop system that cycles the hot liquid through a remote heat exchanger and/or secondary cooling system, and back into the cold plate.
Limitations of single-phase pumped cooling systems
However, in these pumped, single-phase thermal management systems, it’s important to keep the cooling liquid from boiling or changing phases (from a liquid to a gas). If the coolant in your car gets too hot due to a faulty water pump, worn-out radiator, or clogged liquid cooling passages in the engine block, it can boil, at which point the super-hot water vapor causes huge pressure spikes in the system and is unable to transfer heat efficiently. The stereotypical radiator geyser (or a blown coolant hose) can result, and your engine may be permanently damaged. The same thing can happen in your desktop computer tower or server, if the cooling liquid evaporates or boils, creating an air gap in the system and potentially spiking pressure.
Pumped two-phase thermal management systems, on the other hand, are designed specifically to take advantage of the phase change from liquid to gas/vapor, and this change in phase is integral to the improved performance of these cooling systems.
How does a pumped two-phase cooling system work?
The basic cycle or design of a two-phased system is similar in general appearance to a single-phase system. In a two-phase system, subcooled liquid (usually a refrigerant) is pumped from a reservoir or “accumulator” into the location where the hot components are mounted. The heat energy of the components is absorbed into the latent heat of the cooling fluid, and some of the liquid is converted into vapor. This hot liquid-vapor mixture is then pumped to a condenser (a heat exchanger with multiple loops and usually fins) for cooling, where the vapor is fully converted back into a liquid and returned to the accumulator or reservoir, and the cycle repeats.
Image courtesy of ResearchGate.
Subcooling describes sensible heat removed from a saturated liquid/vapor below its boiling point. In simple terms, the liquid coolant becomes subcooled as its temperature continues to drop after it has changed phases from a gas/vapor back into liquid.
“Pumped two-phase cooling merges the features of two-phase cooling and liquid cooling systems, combining the strengths of both cooling technologies,” says Boyd Corporation. “Two-phase cooling employs specialized cold plates to efficiently cool high power equipment by evaporating the working fluid for rapid heat removal from heat sources. The modified liquid system architecture pumps working fluid to reject absorbed heat with a heat exchanger. Coolant condenses, and the system pumps liquid back to the cold plates to repeat the process.”
In Boyd’s example, primarily for electronics (including power electronics) applications, cold plates can function as the condensers, but in other applications with higher heat loads, different types of heat exchangers may be used as condensers.
Advantages of pumped two-phase cooling systems
Thermal management systems designed around coolants or refrigerants that fully or partially change phases allow you to manage more heat, all else being equal, when compared with a non-phase-change system. This is because, when you use a phase-change material, you take advantage of not just the sensible heat of the material, but also the latent heat available across the phase change. We explain this in more detail in our article on phase-change thermal capacitors, though in that case the phase-change in question is from a solid to a liquid and back. But the thermodynamic principles are similar here. When phase change is accounted for and exploited, the seemingly impossible becomes possible.
Pumped two-phase thermal management systems are used where the heat load or size/weight limitations (or both) are beyond what a single-phase system can handle. Let’s explain: When the heat load is increased in a single-phase system, the coolant flow must be increased to compensate. This, in turn, requires a larger (and heavier) pump, which draws more power and takes up more space. If the heat load increases further, we reach a point of diminishing returns where the amount of coolant flow, the power draw, and the size of components becomes prohibitively large.
Two-phase systems typically use refrigerants, which are designed to boil or vaporize at specific temperatures. As the refrigerant comes into contact with the hot components, it boils and changes phases. More heat can be removed via boiling, known as latent heat across the phase change, than via the sensible heat of a single-phase cooling system. This boiling that takes place across the entire evaporator surface provides additional advantages, in that the evaporator itself can display a much more uniform temperature throughout the unit, typically within just a few degrees from the intake to the outlet. This uniformity in temperature is advantageous in many applications. For example, the high-powered lasers used in some directed energy weapons have wavelength emission sensitivity that can be impacted by heat fluctuations.
An additional advantage of pumped two-phase systems is that they don’t require high coolant/refrigerant flow rates, compared to a single-phase system under the same heat load. As a result, smaller pumps requiring less power (and which are lighter and take up less space) can be used to remove a greater amount of heat. In effect, this increases the coefficient of performance of the cooling system. This is important for systems such as aerospace, aviation, or electronics cooling systems that must be extremely compact and require minimal external power.
In one example, an identical heat load is calculated at 80 kW and applied to both a single-phase and a two-phase pumped cooling system. In the single-phase system, a liquid flow rate of 134 liters per minute is required to effectively remove the waste heat, with a pump that uses 5.3 kW of power to drive the liquid at the necessary flow rate. By comparison, an identical 80 kW heat load applied to a pumped two-phase system requires a liquid/vapor flow of just 25 liters per minute, and a pump utilizing just 250 watts of power. This represents an 80% reduction in required flow rate, and a 95% reduction in power demands. That’s not accounting for the added benefits of smaller, lighter components, which are always paramount in aviation and aerospace. With performance gains like that, it’s clear why pumped two-phase thermal management systems have become de rigueur among the aerospace elite.
Bonus: Be sure to check out GS1-EV EagleV, an off-the-shelf combined ECS and battery thermal system we developed for the eVTOL and electric aircraft industries. It’s a good example of pumped two-phase thermal systems architecture in the wild.
–By Jeff Davis, Intergalactic Scribe
Sources:
https://www.boydcorp.com/thermal/liquid-cooling-systems/pumped-two-phase.html