Thermal materials for aerospace: an overview
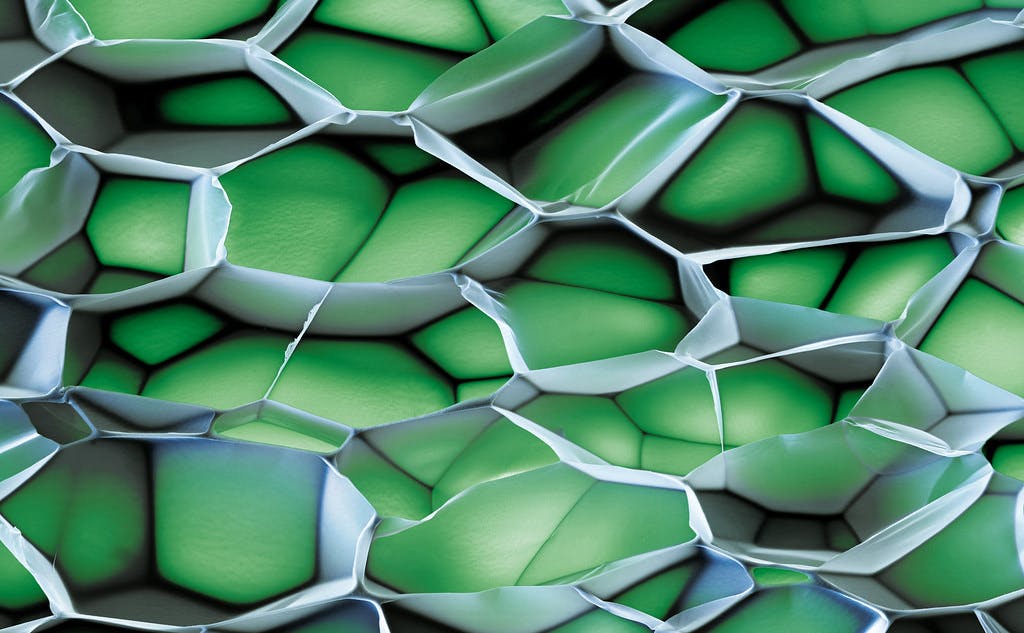
Blog
We’ve said before that aerospace and aviation is all about managing heat. Relatively speaking, getting people and things up in the air is the easy part these days. Keeping hot things cool enough to work—and work reliably—is where things get complicated. Luckily, some super-smart folks have come up with solutions like lightweight heat exchangers and specialized thermal materials (ask about our ultra-cool composite cold plates!) to help keep the cool side cool and the hot side from getting too hot.
There are multiple types of, and applications for, thermal materials in aviation and aerospace. These range from thermal interface materials used in the heat sinks or cold plates of advanced avionics, to modern heat-resistant insulating fabrics used to protect air/spacecraft components from the heat of jet engines or rocket motors, to ablative thermal materials used in external heat shields on re-entry vehicles and some hypersonic vehicles. Additionally, the advanced superalloys used in jet engines and rocket motors are also certainly a category of thermal material, as they have been developed specifically to withstand intense heat, as well as the cracking, corrosion, and degradation that can occur in extreme-heat environments.
Let’s go over some of the common types of thermal materials used in aviation and aerospace.
Advanced thermal insulation or smart fabrics
High-temperature insulation is a type of thermal material commonly used in commercial and military aircraft, as well as eVTOLs and spacecraft. Thermal “blankets,” fabric, ceramic “superwool,” and other heat-resistant insulation are widely used in aerospace and aviation. The heat-management effects of these advanced fabrics and insulation help support safe and reliable function of engines and environmental control systems (ECS), electronics, emission control systems, and weapons systems. Thermal insulation is also often employed as a multi-functional material that helps reduce vibration and lower potentially harmful noise levels throughout an aircraft, in addition to its heat-mitigating effects. Specialized insulation materials span a wide range, from open-cell melamine foam, to calcium silicate panels, to microporous flexible tapes and foils, to specialized fiberglass, vermiculite, mica, silica, metal, or ceramic wools.
High-temperature insulation applications
Jet engines and rocket motors
High-temperature insulation is critical for the protection of sensitive aircraft components from the wide temperature fluctuations resulting from high levels of compression (as the pressure of a gas increases, temperature increases) and the extreme cold of decompression or expansion chambers. Insulation may be used on and/or around jet engines and rocket motors.
Aircraft interiors
Temperature-stabilizing insulation is a key component of effective environmental control systems in aircraft interiors and cabins. Insulation is used to shield air ducts, tubing, and air-cycle systems, as well as paneling for fuselage interior walls, ceilings, and overhead storage compartments.
Thrust reversal systems
Thrust reversal systems are what help slow large airliners and transport planes after landing by rerouting engine exhaust toward the front of the aircraft, effectively redirecting the thrust of the engine. Insulation is used to protect surrounding components and structures from the heat of the exhaust. This thrust reversal happens only momentarily compared to the length of the flight, but without insulation, these redirected, super-hot engine gases would quickly erode surfaces and cook sensitive systems to death.
Electrical components, avionics, and batteries
Many avionics and electronic components used in aviation and aerospace are highly sensitive and need protection from heat, extreme cold, and electromagnetic interference. Specialized thermal material insulation is used to protect electronic instruments, batteries, and auxiliary power units from extreme temperatures as well as interference that could compromise their function. High-temp insulation is also used to insulate against or compartmentalize any electrical fires for enhanced aircraft safety and survivability.
High-temperature insulation is also used to protect the “black boxes” that record key data during any emergencies during flight. The exterior casing of each black box is composed of a highly durable and thermally efficient insulating material, to ensure it can survive violent events and be recovered.
Thermal insulation is also essential to the new generations of electrically powered aircraft, including eVTOLs and air taxis. As we’ve seen in some highly publicized fires of Teslas, hybrid Jeep Wranglers and other e-vehicles, high-powered battery systems generate a lot of heat. Managing and insulating that heat is a primary concern.
Thermal Interface Materials (TIM) for avionics and other electronics in aerospace
Another way thermal materials are used in aviation and aerospace electronics is as a vital component of the heat sinks and/or cold plate cooling systems necessary to keep these devices from destroying themselves (and the aircraft or spacecraft) due to overheating. Thermal interface materials is the term for the thermal materials, compounds, or adhesives used to fill in the microscopic gaps between an electronic component and the cold plate or heat sink attached to it. The more efficient these thermal materials are at conducting heat, the better the heat-shedding capability of the system, and the more reliable the electronics.
Additionally, today’s super-powerful directed-energy weapons, next-gen jammers, and other electronic warfare weapons systems may not require roasty-toasty rockets or jet engines to function, but they still generate immense amounts of heat. More effective shedding and insulating of heat allows greater power and capability of these electronic systems. Proper application of thermal insulation, cooling systems, and thermal interface materials is essential to keep these laser-blasters blasting.
TIM can be composed of multiple materials, but the most recent and most advanced thermal materials being developed and studied for use in aerospace are:
- Polymer matrix composites: Different types of carbon fibers are combined with a variety of thermosetting and thermoplastic resins, including epoxy, cyanate ester, liquid crystal, nylon, polycarbonate, ABS (acrylonitrile butadiene styrene), PBT (polybutylene terephthalate), and polyphenylene sulfide.
- Metal matrix composites: Several types include silicon-carbide-particle-reinforced aluminum, beryllium-particle-reinforced beryllium, carbon-fiber-reinforced aluminum, copper-tungsten, copper-molybdenum, aluminum-silicon, and Invar silver.
- Carbon/carbon composites: These consist of carbon nanofibers, vapor-grown carbon fibers, nano-graphene platelets, pyrolytic graphite, and other carbon/carbon mixes.
In addition to recent research uncovering several promising applications for TIM using nanotechnology (such as carbon nanotubes and graphene nanocomposites), high-thermal-conductivity graphite foams employed as heat sinks are also being developed for aircraft applications.
When properly designed and utilized, thermal interface materials combined with efficient heat sinks or cold plates can effectively manage heat at the device level. If the heat load is balanced with the effectiveness of the materials, it may be possible to eliminate heavier, more complicated heat-management devices and components. When you’re talking about aircraft and spacecraft, weight and size are always a primary consideration.
Ablative thermal materials for extreme high temperatures
Thermally resistant superalloys may resist temperatures up to 3,300°C (6,000°F)—in the case of the Saturn V rocket engines, for example, but they aren’t practical or light enough to be used in heat shielding for vehicles re-entering Earth’s atmosphere. Until some megabrain discovers anti-gravity, the only way we’ve figured out how to do this is by installing refractory insulating heat shields (in the case of the Space Shuttle and Starship) or ablative heat shields on our returning space vehicles. Refractory insulating tiles are usually constructed of high-grade quartz/silica fibers with a layer of insulating ceramic wool underneath. Ablative heat shields are commonly constructed using phenolic-impregnated carbon ablator (PICA), PICA-X, PICA-3, silicone-impregnated reusable ceramic ablator (SIRCA), and AVCOAT, all utilizing different constructions of carbon, silicone, resins, and/or epoxies.
Refractory heat shields reflect about 90% of the heat back into the atmosphere, and the remainder is absorbed by the ceramic wool and other insulating materials beneath the tiles. The tiles may survive multiple trips through re-entry, and are carefully inspected after each use and replaced if needed.
Ablative heat shields are designed of resin-type materials designed to be carried away, disintegrated, or eroded by the intense friction and heat generated by massive speed combined with air. The heat shielding materials on the bottom of space vehicles not only are extremely efficient insulators against heat, but when heated to the 5,000-degrees F (or so) temperatures during re-entry, they essentially “push back” at the heat. The science is extremely complicated and a true understanding involves a detailed knowledge of the various gas models in shock-layer gas physics, but in very simple terms, an ablative heat shield consists of a layer of plastic resin, the outer surface of which is superheated to a gas, which then carries the heat of the compression/shock layer away by convection. An ablative heat shield functions as a sacrificial surface, creating a boundary layer utilizing the “blowing” of gaseous reaction products from the burning resins in the heat shield material, which lifts the hot shock layer gas away from the heat shield’s outer wall, creating a much cooler boundary layer as long as the temperatures and speeds are sufficient to maintain that gas barrier.
In some circles ablative materials are favored when they are capable of creating a sturdy “char layer” that protects the inner material, maintaining its integrity and slowing thermal degradation.
Any vehicle designed to carry humans and/or technology into space and return safely will need to take advantage of all of the above types of thermal materials, both inside and outside of the spacecraft, to ensure success.
–By Jeff Davis, Intergalactic Scribe
Sources:
https://www.rcftechnologies.com/high-temp-materials-in-aviation/
https://mid-mountain.com/aerospace-insulation-fabrics-for-vibration-and-temperature/
https://amorimcorkcomposites.com/en-us/materials-applications/aerospace/
https://www.polytechinc.com/industries/aviation-aerospace
https://www.morganthermalceramics.com/en-gb/industries/aerospace/
https://www.aerospacemanufacturinganddesign.com/article/amd1212-electronics-thermal-management/
https://www.promat.com/en-us/industry/technologies/textiles-and-wools/